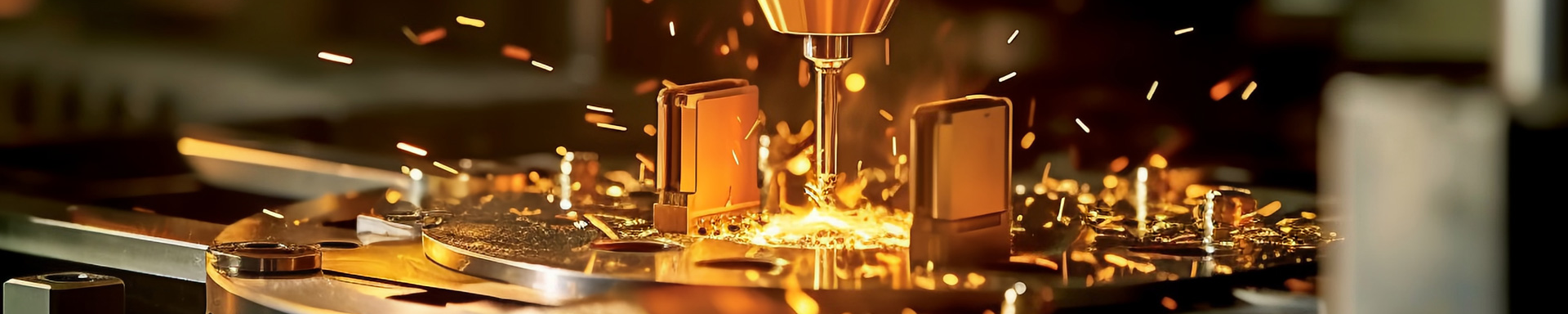
Custom Shape Punch Die Inserts
2024-11-28 16:46Design Flexibility and Customization
The most compelling advantage of custom shape punch die inserts is their adaptability. Unlike standard punches limited to pre-defined shapes, custom inserts can be engineered to match virtually any conceivable geometry. This opens up a world of possibilities for manufacturers, enabling the production of parts with unique features that differentiate their products or enhance their functionality. The design process typically involves close collaboration between the manufacturer and the insert supplier, ensuring the final product precisely meets the specifications and tolerances required.
This level of customization extends beyond simple shapes. Features such as intricate internal cutouts, tapered holes, and complex profiles are easily achievable. Furthermore, the inserts can be designed to accommodate a variety of materials, from thin gauge sheet metal to thicker, more robust materials, requiring only adjustments to the die and press settings. This eliminates the need for costly and time-consuming secondary operations, such as machining or laser cutting, thereby significantly reducing overall production costs.
Material Selection and Durability
The material used in the manufacturing of custom shape punch die inserts is critical to their performance and longevity. High-speed tool steels are commonly employed due to their exceptional hardness, wear resistance, and ability to withstand the high pressures and repeated impacts associated with stamping operations. The specific steel grade selected will depend on the application, material being stamped, and desired lifespan of the insert. Careful consideration of factors such as the material’s tensile strength, compressive strength, and resistance to fatigue is essential to ensure the insert can consistently perform to exacting standards without premature failure.
Beyond tool steels, other materials such as carbide may be employed for applications requiring exceptionally high wear resistance or when stamping extremely hard materials. The choice of material directly impacts the overall cost and longevity of the insert, with harder, more durable materials often commanding a premium but offering a greater return on investment through extended lifespan and reduced downtime.
Manufacturing Process and Tolerances
The creation of custom shape punch die inserts typically involves a sophisticated manufacturing process. This often includes Computer Numerical Control (CNC) machining, which offers exceptional precision and the capability to create intricate shapes with tight tolerances. Advanced techniques such as wire EDM (Electrical Discharge Machining) might be utilized for particularly complex geometries or delicate features. The manufacturer will usually employ stringent quality control measures throughout the production process to ensure the final product meets the specified dimensions and tolerances.
Achieving tight tolerances is crucial for the proper functioning of the insert and the quality of the stamped parts. The ability to produce inserts with minimal variation in shape and size translates to consistent part quality and reduces the likelihood of rejects. Modern manufacturing techniques allow for the creation of inserts with tolerances as tight as a few micrometers, ensuring exceptional precision and repeatability in the stamping process.
Cost-Effectiveness and Return on Investment
While the initial cost of custom shape punch die inserts may be higher than standard punches, the long-term cost-effectiveness is often significant. The elimination of secondary operations, increased production efficiency due to faster cycle times, and reduced material waste all contribute to substantial cost savings over the lifespan of the insert. The improved consistency in part quality further reduces waste from rejected parts and rework.
The return on investment (ROI) for custom shape punch die inserts is heavily dependent on the specific application and production volume. However, for high-volume production runs of parts with complex geometries, the ROI can be exceptionally high, justifying the initial investment many times over through reduced labor costs, material savings, and increased production efficiency. A thorough cost-benefit analysis is crucial to assess the viability of this investment in a particular manufacturing context.