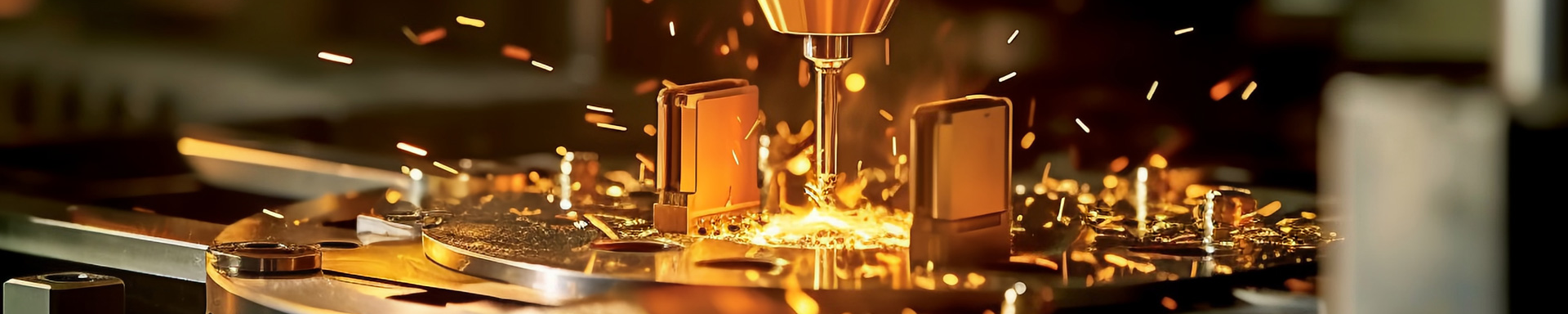
Aircraft Rubber Parts High Quality
2024-12-04 15:52Material Selection: The Foundation of Quality
The foundation of any high-quality aircraft rubber part lies in the meticulous selection of raw materials. Manufacturers don't simply use any rubber; they carefully choose specific compounds tailored to withstand the extreme conditions experienced during flight. Factors like temperature extremes, exposure to oils and fuels, ozone degradation, and intense UV radiation all demand specialized rubber formulations. Common choices include nitrile rubber (NBR) for its resistance to oils and fuels, silicone rubber for its high-temperature resistance, and fluorosilicone rubber for its exceptional chemical resistance. The precise composition of these materials, often involving a blend of different polymers and additives, is crucial in determining the final product's performance and lifespan. Furthermore, rigorous quality control measures are implemented at every stage, from the sourcing of raw materials to the final inspection of the finished part, ensuring only the highest-grade components are used.
Beyond the base rubber, additives play a critical role in enhancing specific properties. These can include fillers that improve strength and durability, antioxidants to combat degradation, and plasticizers to enhance flexibility. The careful balancing of these additives is a key factor in achieving the desired performance characteristics, optimizing the rubber compound for the specific application. For example, a rubber seal used in a high-pressure hydraulic system requires vastly different properties than a rubber mount designed to absorb vibrations in an engine. The selection process is thus highly specific and driven by rigorous testing and analysis to ensure the final product meets and surpasses demanding aviation standards.
Manufacturing Precision: Ensuring Dimensional Accuracy
The manufacturing process of high-quality aircraft rubber parts demands extreme precision. Unlike mass-produced rubber components, these parts must adhere to stringent tolerances to ensure a perfect fit and reliable functionality within the aircraft system. Advanced manufacturing techniques are employed, ranging from precise molding processes using high-pressure injection molding or compression molding to sophisticated extrusion techniques for creating complex shapes and profiles. These processes require meticulously calibrated machinery and highly skilled operators to guarantee consistent product quality and dimensional accuracy.
Beyond the core molding or extrusion processes, post-processing steps are often crucial. These can include trimming, deburring, and inspection using advanced techniques like automated optical inspection (AOI). AOI systems allow for rapid and accurate detection of any flaws or deviations from the specified dimensions, ensuring that only perfectly formed parts proceed to the next stage. This commitment to precision is non-negotiable; even minor imperfections can compromise the functionality and safety of the component, potentially leading to serious consequences.
Testing and Quality Control: Rigorous Standards
The aviation industry operates under the strictest safety regulations. Consequently, aircraft rubber parts undergo rigorous testing procedures to ensure they meet and exceed these standards. Tests are designed to simulate the extreme conditions encountered during flight, including temperature cycling, exposure to chemicals, and fatigue testing to assess durability under stress. These tests involve measuring key performance indicators, such as tensile strength, elongation, compression set, and resistance to various environmental factors.
Beyond these standardized tests, specific tests might be tailored to the particular application of the rubber part. For example, a seal intended for use in a fuel system might undergo permeation testing to assess its ability to prevent fuel leakage. Similarly, a vibration dampener would be subjected to dynamic tests to evaluate its effectiveness in reducing unwanted vibrations. This meticulous approach to testing and quality control guarantees that each aircraft rubber part operates reliably and safely, contributing to the overall integrity and safety of the aircraft.
In conclusion, the pursuit of high quality in aircraft rubber parts isn't merely a matter of satisfying industry standards; it's a fundamental commitment to ensuring the safety and reliability of air travel. From the careful selection of materials to the rigorous testing protocols, every step in the manufacturing process reflects this dedication. The seemingly simple rubber component plays a crucial, often unseen role in the complex machinery that keeps us soaring above the clouds.