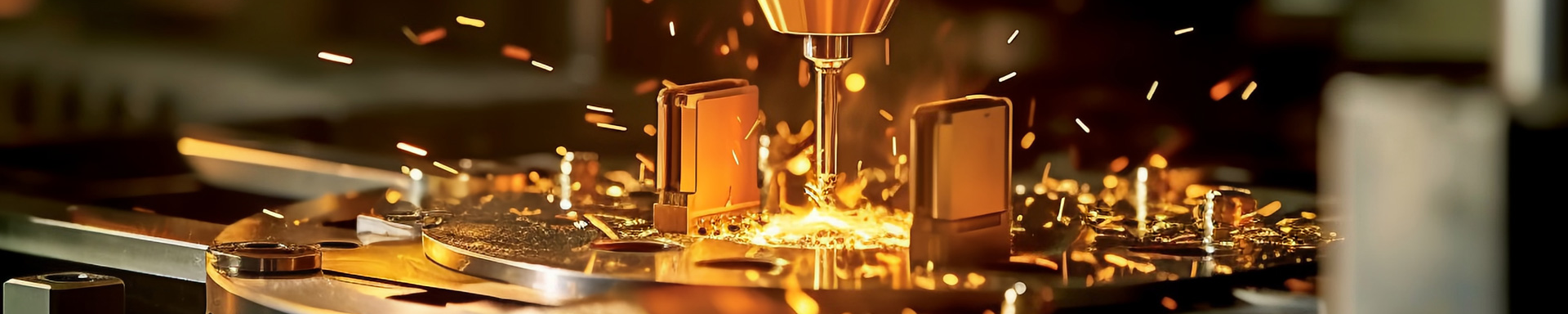
Durability and Efficiency in Punching and Shearing Dies
2025-01-08 14:09Material Selection for Enhanced Durability
The longevity of a punching or shearing die is intrinsically linked to the material it's made from. High-strength tool steels, such as high-speed steel (HSS), powder metallurgy high-speed steel (PM-HSS), and various grades of carbide, are frequently employed due to their exceptional hardness, wear resistance, and toughness. HSS offers a good balance of properties and is widely used for general-purpose applications. PM-HSS boasts superior hardness and wear resistance, extending die life significantly, particularly when dealing with abrasive materials. Carbide, on the other hand, provides the highest hardness and wear resistance, making it ideal for high-volume production runs or when cutting exceptionally hard materials.
The selection of a suitable material isn't solely based on hardness. Toughness is equally important, as it determines the die's ability to withstand impact loads and prevent fracture. Brittle materials might exhibit superior hardness but lack the resilience to absorb shocks, leading to premature failure. Therefore, a careful balance between hardness and toughness is crucial, often necessitating sophisticated material analysis and testing to determine the optimal material for a specific application considering factors like the material being processed and the production volume.
Optimized Die Design for Improved Efficiency
The design of the die plays a critical role in both its durability and efficiency. Several key aspects need careful consideration. Firstly, the geometry of the cutting edges directly affects the shearing process. Sharp, precisely ground cutting edges minimize friction and reduce the force required for cutting, leading to higher efficiency and reduced wear on the die. Secondly, proper clearance between the punch and die is essential. Insufficient clearance can lead to excessive friction, increased wear, and even die breakage. Conversely, excessive clearance can result in burrs and inaccurate cuts.
Furthermore, the design should incorporate features that facilitate easy maintenance and replacement. Modular designs allow for the easy replacement of worn components instead of replacing the entire die, significantly reducing downtime and costs. Similarly, designs that incorporate features for chip evacuation are crucial for preventing chip buildup, which can lead to damage to the die and compromised product quality. Finally, incorporating features such as lubrication channels or coatings can minimize friction and wear, extending the die's service life.
Lubrication and Cooling for Extended Die Life
Appropriate lubrication and cooling are vital for maintaining both the durability and efficiency of punching and shearing dies. Lubricants reduce friction between the die and the workpiece, minimizing wear and tear on the cutting edges. The choice of lubricant depends on several factors, including the material being cut, the die material, and the operating conditions. Water-based lubricants are commonly used due to their environmentally friendly nature and effectiveness in dissipating heat. However, oil-based lubricants might be preferred in situations requiring superior lubrication properties.
Effective cooling is equally crucial, especially during high-speed or high-volume operations. Excessive heat generated during the cutting process can lead to premature wear, reduced tool life, and even thermal cracking of the die. Cooling systems, employing methods such as coolant sprays or circulating fluids, effectively manage heat dissipation and maintain optimal operating temperatures, thus significantly contributing to die longevity and consistent performance.
Regular Maintenance and Inspection for Proactive Management
Proactive maintenance and regular inspections are indispensable for maximizing the lifespan and efficiency of punching and shearing dies. Regular sharpening or replacement of worn cutting edges is crucial for maintaining accuracy and efficiency. Careful inspection for cracks, chips, or other signs of damage should be performed regularly, allowing for timely repairs or replacements before catastrophic failure occurs. This preventive maintenance approach significantly reduces unexpected downtime and prevents costly repairs or replacements caused by neglecting minor issues.
Establishing a robust maintenance schedule, which includes routine cleaning, lubrication, and inspection, is key to ensuring optimal die performance. Proper documentation of maintenance activities, including dates, procedures, and observations, allows for tracking die performance and predicting potential failures. Implementing a system for monitoring die wear, perhaps through measuring tool wear or force, enables early detection of deterioration and helps in optimizing maintenance schedules for maximum efficiency and reduced downtime.
Conclusion
The durability and efficiency of punching and shearing dies are critical factors determining the success of any sheet metal manufacturing process. By carefully considering material selection, optimizing die design, implementing appropriate lubrication and cooling systems, and adhering to a rigorous maintenance schedule, manufacturers can significantly extend die life, enhance production efficiency, and ensure consistent product quality. Investing in advanced technologies and best practices in die maintenance translates directly into cost savings, reduced downtime, and a more competitive advantage in the market.