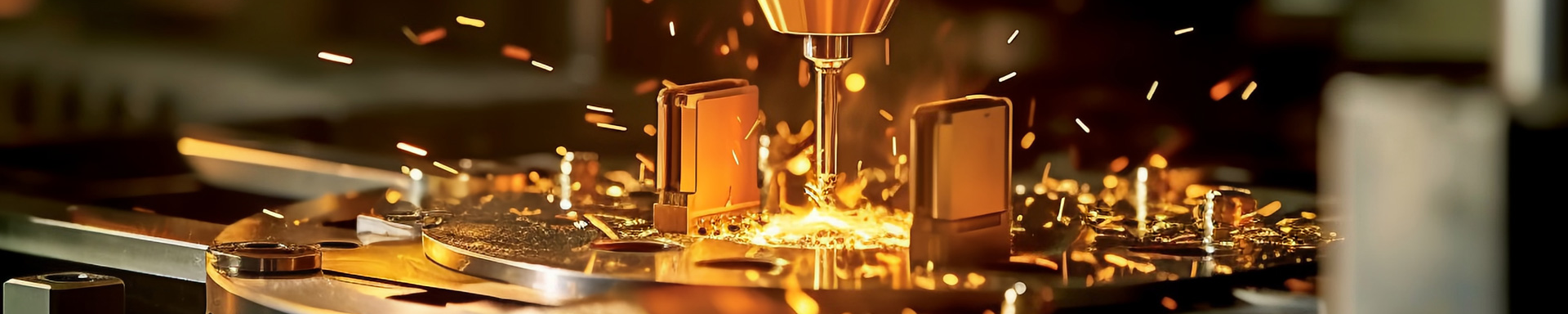
Durable Rubber Products for Aircraft Applications
2024-12-17 14:50Sealing Solutions: O-rings, Gaskets, and Seals
One of the most prevalent applications of durable rubber in aircraft is in sealing systems. O-rings, gaskets, and seals are vital for preventing leaks of fluids, gases, and air pressure, ensuring the proper functioning of hydraulic systems, fuel systems, and pneumatic systems. These rubber components create airtight and liquid-tight barriers, protecting sensitive equipment from contamination and maintaining optimal pressure within systems.
The types of rubber used in these applications vary depending on the specific requirements. For instance, nitrile rubber (NBR) is often chosen for its resistance to fuels and oils, while fluorosilicone rubber (FVMQ) exhibits excellent resistance to high temperatures and various chemicals. Ethylene propylene diene monomer rubber (EPDM) is another popular choice due to its resistance to ozone, weathering, and extreme temperatures, making it suitable for external sealing applications.
The design and manufacturing of these seals are critical. Precision engineering ensures a perfect fit and optimal sealing performance. Factors like the hardness of the rubber, its cross-sectional shape, and the specific operating conditions are all carefully considered during the design process.
Vibration Damping and Shock Absorption
Aircraft are subjected to significant vibrations and shocks during flight, from engine vibrations to turbulence and landing impact. Durable rubber products play a crucial role in mitigating these forces, protecting sensitive electronics, instruments, and structural components from damage.
Rubber mounts and vibration isolators are strategically placed throughout the aircraft to absorb vibrations and dampen shocks. These components are typically made from specialized rubber compounds that offer high damping properties and can withstand repeated cycles of stress without degrading.
The selection of the appropriate rubber compound for vibration damping applications depends on the frequency and amplitude of the vibrations, as well as the temperature and environmental conditions. Natural rubber, for example, exhibits excellent damping properties at lower frequencies, while synthetic rubbers like silicone and neoprene offer better performance at higher frequencies.
Hose and Tubing Applications
Flexible rubber hoses and tubing are essential for conveying fluids and gases throughout the aircraft. These applications range from fuel lines and hydraulic lines to oxygen supply systems and air conditioning ducts.
The rubber used in these hoses must be resistant to the specific fluids being transported, as well as to the operating temperatures and pressures. Furthermore, the hose construction must be robust enough to withstand flexing and vibrations without leaking or cracking. Reinforcement materials like braided fabric or wire mesh are often incorporated into the hose structure to enhance its durability and pressure resistance.
Specialized rubber compounds like fluoroelastomers and perfluoroelastomers are often chosen for their exceptional resistance to a wide range of chemicals, fuels, and extreme temperatures, making them ideal for demanding hose and tubing applications in aircraft.
Other Applications and Future Trends
Beyond sealing, vibration damping, and hose applications, durable rubber products find various other uses in aircraft. They are used in window seals, door seals, electrical insulation, and even in tires. The unique properties of rubber make it an indispensable material in countless aircraft components.
The future of durable rubber products for aircraft applications is promising. Ongoing research and development are focused on creating even more resilient and high-performing rubber compounds. Nanotechnology and the incorporation of advanced materials are leading to the development of lighter, stronger, and more environmentally friendly rubber products. These advancements will further enhance the safety, efficiency, and sustainability of air travel.
The demanding nature of the aerospace industry requires materials that can perform reliably under extreme conditions. Durable rubber products, through their versatility, resilience, and specialized properties, fulfill a critical role in ensuring the continued safety and performance of aircraft, contributing significantly to the advancements in aviation technology.