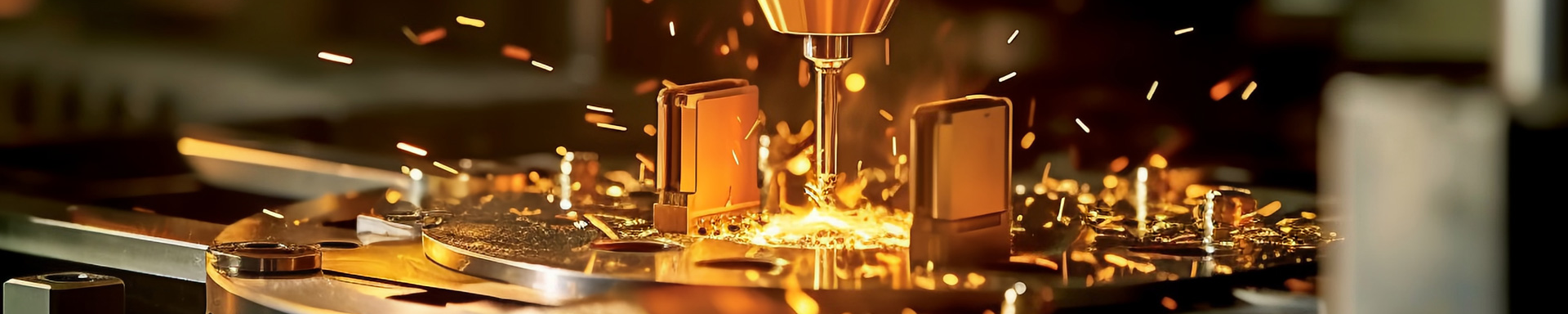
Understanding Punching and Shearing Die Processes
2025-01-08 14:12Punching Processes: A Deep Dive
Punching involves using a precisely shaped punch to force a piece of metal through a die, creating a hole or a specific shape. This process relies on compressive forces to shear the material along the punch's edge. The geometry of the punch and die is paramount; the clearance between them, typically a small fraction of the material thickness, dictates the quality of the cut. Too much clearance can lead to ragged edges and burrs, while too little can cause excessive force requirements, tool wear, and potential fracturing. The process is relatively fast and efficient, making it suitable for high-volume production.
Punching is widely used for creating holes in sheet metal, often employing progressive dies for complex part geometries. Progressive dies allow multiple operations—punching, bending, forming—to be performed sequentially in a single pass. This enhances efficiency significantly, but designing and manufacturing these dies requires considerable expertise. Moreover, the selection of the punch and die material itself impacts the longevity and performance of the tools. High-strength tool steels are typically preferred for their durability and resistance to wear and tear.
Material properties play a crucial role in the success of punching. Thicker materials require more force, necessitating larger and stronger presses. Brittle materials are more prone to cracking, demanding careful consideration of punch design and press parameters. Ductile materials, while easier to punch, can form burrs, necessitating secondary operations like deburring to ensure surface finish quality. Understanding the material's yield strength, tensile strength, and ductility is essential for accurate process planning and optimization.
Shearing Processes: Precision Cutting
Shearing, in contrast to punching, uses a pair of blades to cut through a sheet of metal. The blades are precisely aligned and positioned, and a shear force is applied to cause the metal to fracture along the blade's edge. Unlike punching, shearing typically produces a straighter, cleaner cut, particularly with thinner materials. The shearing process relies on the controlled application of tensile and compressive stresses at the cutting edge, creating a fracture zone that propagates through the material.
The angle of the shearing blades is carefully designed to optimize the cutting process. A slight angle facilitates a clean separation of the material, reducing burr formation. The blade sharpness and material quality also directly influence the cut quality. Dull blades or poorly maintained shearing machines can result in jagged edges and increased material waste. Regular blade sharpening and maintenance are crucial for maintaining the efficiency and accuracy of the shearing process.
Shearing is frequently employed for blanking operations—cutting out individual parts from a larger sheet—and slitting operations—cutting a sheet into narrower strips. Blanking dies require precise design and manufacturing tolerances to ensure consistent part dimensions. Slitting dies, often used in continuous coil processing, demand high durability and resistance to wear given the continuous contact with the metal sheet. Material selection for shearing blades is crucial; materials must offer high hardness, wear resistance, and toughness.
Punching vs. Shearing: A Comparative Analysis
Both punching and shearing are effective sheet metal cutting processes, but their suitability depends on several factors. Punching is often preferred for creating holes or intricate shapes in smaller quantities, while shearing excels in high-volume production of blanks or slits. Punching typically produces smaller burrs, especially with thinner materials, whereas shearing can produce larger burrs if the blade angles or sharpness aren't optimal. The choice between the two methods often involves considering the complexity of the part, required precision, production volume, and overall cost-effectiveness.
The selection of the appropriate process also necessitates considering the available machinery and tooling. Punching presses range from small benchtop machines to large, high-capacity industrial presses. Shearing machines also come in various sizes and configurations, including guillotines and rotary shears. The cost of acquiring and maintaining this equipment is a significant factor in the overall process economics. Furthermore, factors such as material thickness, material type, desired surface finish, and tolerances all influence the final selection of punching or shearing.
In conclusion, understanding punching and shearing die processes requires a multi-faceted approach encompassing the mechanics of each process, the intricacies of tool design and material selection, and the careful consideration of process parameters. By appreciating the nuances of these fundamental sheet metal fabrication techniques, manufacturers can optimize production efficiency, enhance product quality, and minimize waste, leading to cost savings and improved competitiveness in the market.