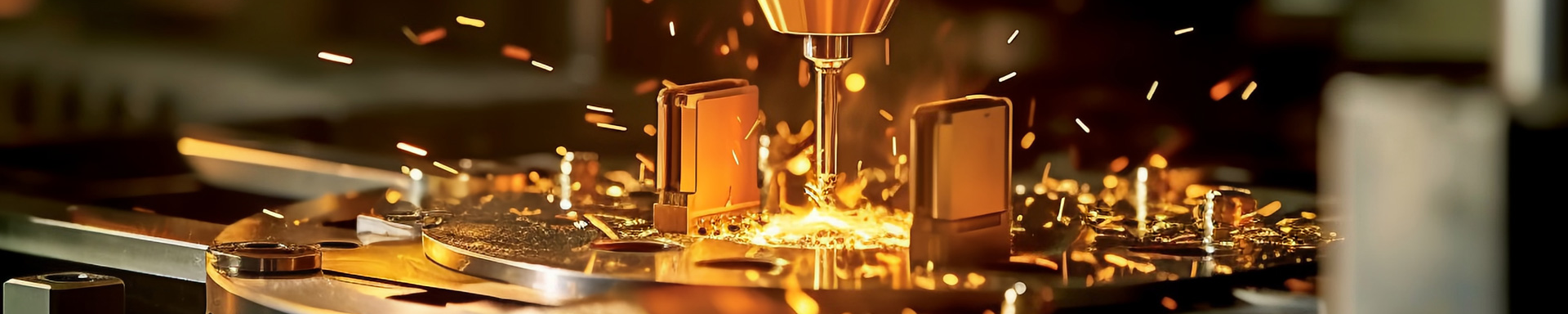
Understanding the Benefits of Moulding Injection
2024-11-20 15:57Understanding the benefits of injection molding requires delving into a manufacturing process that has revolutionized countless industries. From the ubiquitous plastic bottle to intricate automotive components, injection molding's versatility and efficiency have made it a cornerstone of modern manufacturing. This exploration will unveil the key advantages this method offers, highlighting its impact on cost, quality, and overall production efficiency.
High Production Volume and Speed
One of the most compelling benefits of injection molding is its unparalleled ability to produce high volumes of identical parts rapidly. Unlike many other manufacturing techniques, the process is highly automated. Once the mold is prepared, the machine cycles continuously, injecting molten material and ejecting finished parts at impressive speeds. This translates directly into shorter lead times and significantly increased output compared to methods like hand-casting or machining. The consistency of the process also ensures a uniform product, minimizing variations that could occur in manual processes.
This high-speed production is particularly advantageous for mass-produced items. Think of the billions of plastic bottle caps or disposable cutlery produced annually – injection molding is the only practical method capable of handling such immense demands. The automation minimizes labor costs, further enhancing its economic appeal for large-scale production runs.
Exceptional Precision and Repeatability
Injection molding's precision is another key advantage. The meticulously crafted molds allow for the creation of parts with extremely tight tolerances. This means the dimensions and features of each produced part are consistent and accurate, resulting in superior quality and functionality. The process minimizes human error, ensuring that each piece conforms to the specified design parameters.
This repeatability is crucial for industries requiring high levels of quality control. For example, in the medical device industry, precise dimensions and consistent material properties are critical for the safe and effective functioning of implants or diagnostic tools. Injection molding's ability to deliver these qualities makes it an ideal choice for such applications.
Versatility in Material and Design
The adaptability of injection molding extends beyond production speed and precision. A vast range of materials can be used, from common thermoplastics like polypropylene and polyethylene to more specialized materials such as engineering plastics with enhanced strength, durability, or heat resistance. This versatility allows manufacturers to select the optimal material for a specific application, maximizing performance and longevity of the final product.
Furthermore, the design possibilities are virtually limitless. Complex shapes, intricate details, and internal features can be readily incorporated into the mold design. Undercuts, threads, and snap-fit features are easily achievable, reducing the need for secondary assembly processes and further streamlining production.
Cost-Effectiveness in the Long Run
While the initial investment in mold creation can be substantial, injection molding proves highly cost-effective in the long run, especially for high-volume production. The automated nature of the process significantly reduces labor costs, and the high production speed minimizes manufacturing time. The consistent quality reduces waste due to defects, further contributing to cost savings.
The amortized cost of the mold over numerous production cycles makes it a financially sound option for large production runs. Moreover, advancements in mold technology are constantly improving efficiency and reducing the overall cost of production.
Customization and Prototyping Capabilities
Although often associated with mass production, injection molding also offers benefits for prototyping and customized production runs. The creation of molds allows for relatively quick and cost-effective production of prototypes for testing and refinement before large-scale manufacturing commences. Modifications to the mold design can also be implemented relatively easily, allowing for quick adjustments and iterative improvements.
This flexibility makes injection molding suitable for both large-scale manufacturing projects and smaller-scale specialized productions. The ability to produce customized parts, even in smaller quantities, opens up opportunities for niche markets and specialized applications.
In conclusion, the benefits of injection molding extend across numerous aspects of the manufacturing process. Its ability to achieve high-volume production, exceptional precision, material versatility, and long-term cost-effectiveness makes it a dominant force in modern manufacturing, contributing significantly to the efficiency and quality of countless products we use daily.