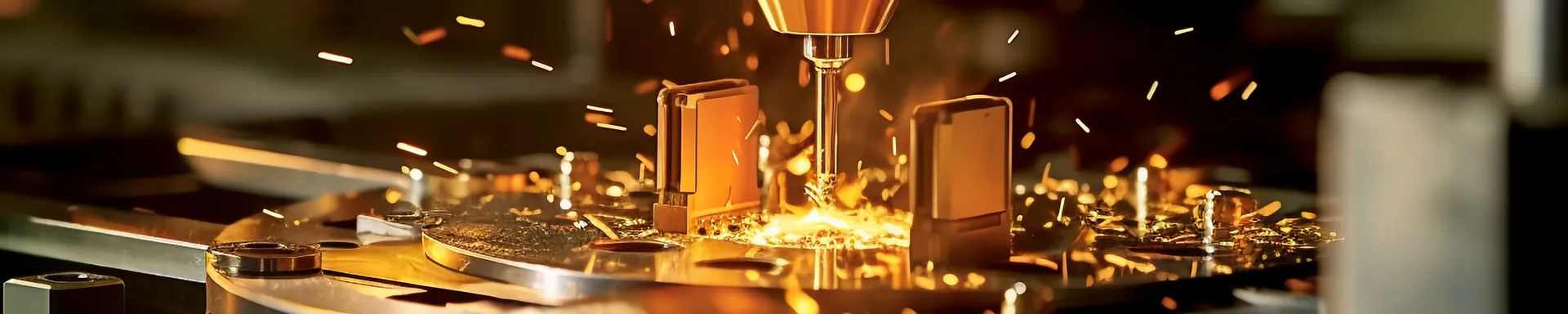
- Home
- >
- Products
- >
- Bottle Stack Mould
- >
Bottle Stack Mould
Bottle stack moulds are commonly used in industries such as beverage, cosmetics, and household products, where high-volume production of plastic bottles is required. They are designed to be durable and withstand the high pressures and temperatures involved in the injection moulding process.
- Information
Die stacking is suitable for mass production.
Stacking mould technology:
Stack mold is a cutting-edge technology in the development of today's plastic mold industry, and the cavity is distributed in 2 or more levels, in a superimposed arrangement. Simply put, the laminated mold is equivalent to placing multiple pairs of single-layer molds together and installing them on an injection molding machine for injection molding production
Usually, when the injection molding machine uses a single-layer plastic injection mold, its own injection volume and opening stroke only use 20% to 40% of the rated injection molding machine, which does not give full play to the performance of the injection machine, and the laminated injection mold can be used on the basis of not increasing the clamping force. Under the condition of the same 1 injection machine and 1 operator, the output can be multiplied according to the number of layers, which can greatly improve the production efficiency and equipment utilization rate, and can save production costs and labor costs
Application scenario:
Previous application scenarios: Molds with a large number of cavities, such as daily necessities, cosmetics, and medical products, are now gradually being used in auto parts molds.
Classification of stack moulds:1) Common laminated mold
Two-layer mold
3-layer mold
4-layer mold
Up to 10 floors
2) Rotate the laminated mold
Double sides rotate 180 degrees each time
Double layer 4 sides each 90 degree rotation lean craft
3 layers 2 sides (180 degrees per rotation)+4 sides (90 degrees per rotation)
Stack mould design considerations:
1) The main nozzle can not go out of the guide sleeve after the mold is opened, and attention should be paid to the reasonable setting of the length of the main nozzle and the mold opening stroke;
2) It is necessary to check the maximum opening stroke and maximum plasticizing amount of the injection molding machine;
3) The pre-molding efficiency of the injection device should be high;
4) The injection rate should be increased appropriately;
5) Pressure release of hot runner melt; 6) Deal with the relationship between cavity layout and main nozzle.