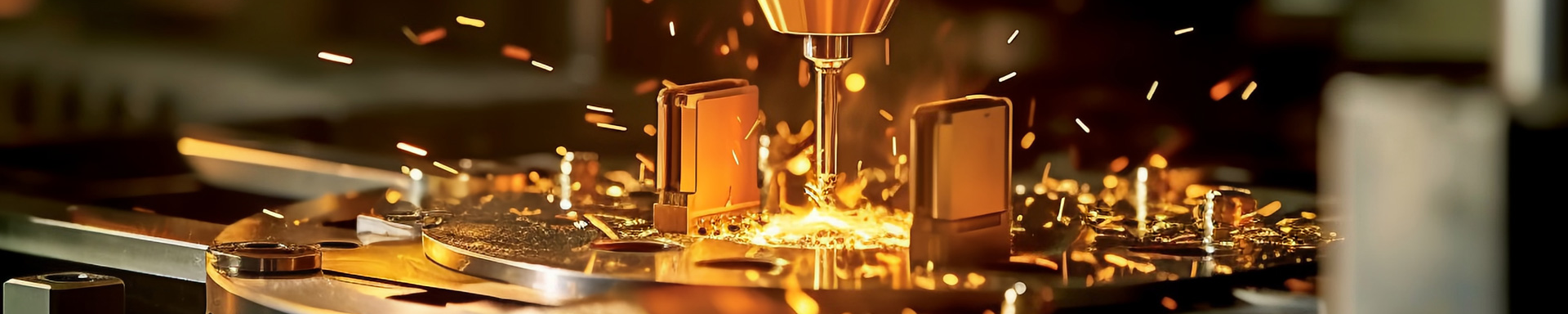
Precision Shape Punch Die Inserts
2024-11-28 16:54Material Selection and its Impact
The material chosen for a precision shape punch die insert directly impacts its lifespan, performance, and the quality of the stamped part. Common materials include tool steels like high-speed steel (HSS), powder metallurgy (PM) tool steels, and carbide. HSS offers a good balance of strength, toughness, and cost-effectiveness, making it suitable for a wide range of applications. However, its wear resistance may be limited compared to other options. PM tool steels boast enhanced strength and wear resistance due to their controlled microstructure, resulting in longer tool life and improved dimensional accuracy. Carbide inserts, while significantly more expensive, provide exceptional hardness and wear resistance, ideal for high-volume production runs involving extremely hard materials or intricate geometries.
The selection process also considers factors beyond material type. The specific grade of steel or carbide, heat treatment processes, and surface coatings all play significant roles in optimizing the insert's performance and extending its service life. For instance, a specialized coating like titanium nitride (TiN) can significantly improve wear resistance and reduce friction, leading to enhanced accuracy and increased production rates. The choice of material is therefore a crucial engineering decision, carefully balancing cost, durability, and the specific requirements of the stamping operation.
Design Considerations and Geometrical Precision
The design of a precision shape punch die insert is far from arbitrary. It must accurately reflect the desired shape of the final stamped part while considering factors such as material thickness, required tolerances, and the overall stamping process. Computer-aided design (CAD) software plays a crucial role in this process, enabling precise modeling and simulation of the insert's performance before actual manufacture. This minimizes the risk of design flaws and allows for efficient optimization.
Geometrical precision is paramount. Minute variations in the insert's dimensions can lead to significant deviations in the stamped part, potentially rendering it unusable. Advanced manufacturing techniques like Electrical Discharge Machining (EDM) and laser cutting ensure the highest levels of accuracy, enabling the creation of complex shapes and extremely tight tolerances. The design process also includes considerations for clearance, shear, and bending radii to ensure efficient and consistent stamping without damaging the insert or the workpiece.
Manufacturing Processes and Quality Control
The production of precision shape punch die inserts requires advanced manufacturing capabilities. Techniques such as EDM, laser cutting, and grinding are commonly employed to achieve the required dimensional accuracy and surface finish. EDM, in particular, excels at producing intricate shapes and fine details, often used to create intricate features within the insert's geometry. Grinding processes are crucial for achieving the necessary surface finish, which directly impacts the quality of the stamped parts and the longevity of the insert itself.
Rigorous quality control measures are essential throughout the manufacturing process. Dimensional inspections using coordinate measuring machines (CMMs) ensure that the insert conforms precisely to the design specifications. Surface roughness measurements are also performed to verify the quality of the surface finish. These quality control steps are vital in ensuring the consistent production of high-quality inserts, reducing downtime and improving the overall efficiency of the stamping operation.
Applications Across Diverse Industries
The applications of precision shape punch die inserts span a wide array of industries. In the automotive sector, they are used to create complex parts for vehicles, from body panels and chassis components to intricate internal mechanisms. The electronics industry utilizes these inserts to produce connectors, terminals, and various other small but critical components. Other sectors such as appliance manufacturing, aerospace, and medical device production also rely heavily on metal stamping, with precision shape punch die inserts playing a key role in their manufacturing processes
The versatility of these inserts allows for the creation of a vast range of shapes and sizes, making them adaptable to the specific needs of each industry. From simple shapes to highly complex geometries, these inserts ensure that metal stamping remains a cost-effective and efficient method for producing high-volume, high-precision parts.