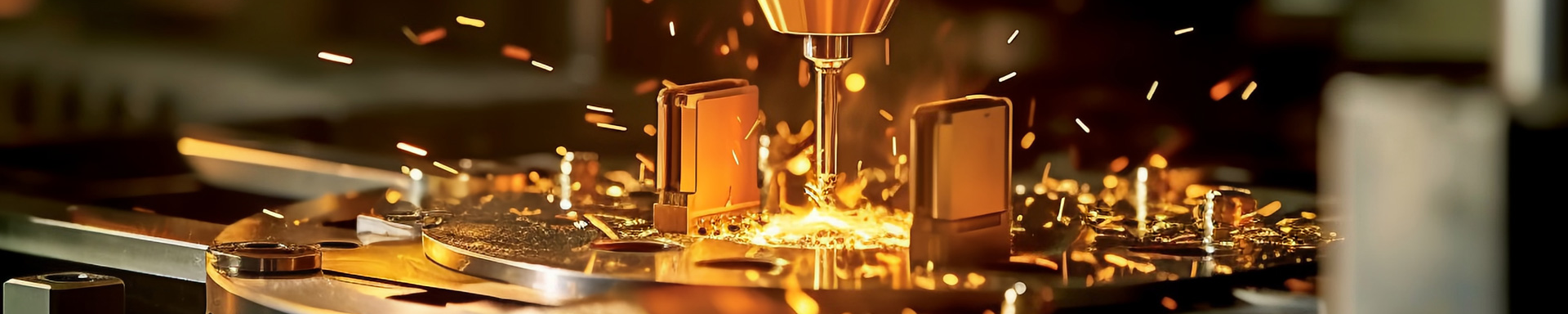
Advanced Moulding Injection Process Optimization Guide
2024-11-20 16:10The relentless pursuit of efficiency and quality in manufacturing has propelled the need for comprehensive guides dedicated to optimizing complex processes. One such process, crucial to countless industries, is injection molding. The intricacies involved, from material selection to intricate mold design and precise machine parameters, demand meticulous control for achieving optimal results. This is where an *Advanced Moulding Injection Process Optimization Guide* becomes invaluable. Such a guide isn't just a collection of best practices; it's a roadmap for navigating the complexities of injection molding, enabling manufacturers to reduce costs, improve product quality, and enhance overall productivity. This exploration will delve into the key aspects covered within such a guide, providing insights into its potential to revolutionize your injection molding operation.
Understanding the Fundamentals: Material Selection and Mold Design
An effective optimization guide begins with a solid foundation. This includes a detailed understanding of the various thermoplastic and thermoset materials available, their properties, and their suitability for specific applications. The guide should provide clear criteria for material selection, considering factors like melt flow index, tensile strength, impact resistance, and chemical resistance. Understanding these characteristics is fundamental to achieving the desired product properties and preventing defects.
Equally crucial is a thorough examination of mold design. The guide would cover topics such as gate location and type, runner design, cooling channels, and ejection systems. The impact of these design choices on filling behavior, part quality, and cycle time is critically analyzed. Furthermore, advanced design concepts like hot runner systems, which can significantly improve efficiency and reduce material waste, would be explored in detail.
Process Parameter Optimization: Achieving Precision and Consistency
The injection molding process itself is governed by a complex interplay of parameters. An advanced optimization guide wouldn't simply list these parameters; it would provide a deep understanding of their interdependence and impact on the final product. This includes a thorough discussion of injection pressure, melt temperature, mold temperature, holding pressure, and injection speed. The guide should highlight the importance of precise control and monitoring of these parameters, emphasizing the use of sensors and data acquisition systems for real-time feedback.
Furthermore, it would discuss advanced techniques such as process capability analysis and statistical process control (SPC). These techniques allow manufacturers to identify and reduce process variations, leading to consistent product quality and reduced scrap rates. The guide might include practical examples and case studies demonstrating how these techniques can be implemented to improve efficiency and yield.
Defect Analysis and Troubleshooting: Identifying and Resolving Issues
No injection molding process is perfect. An advanced guide recognizes this reality and provides comprehensive strategies for identifying and rectifying common defects. This includes a detailed catalog of potential defects, such as short shots, sink marks, weld lines, and warpage, along with their corresponding causes and corrective actions. Detailed illustrations and diagnostic flowcharts would aid in quick identification of the root causes.
Beyond simply listing potential problems, a truly advanced guide would incorporate predictive modeling and simulation techniques. These allow manufacturers to anticipate potential issues before they occur, reducing downtime and improving overall efficiency. By utilizing simulation software, manufacturers can virtually test different process parameters and mold designs, optimizing the process before physical production begins.
Automation and Advanced Technologies: Embracing Industry 4.0
The modern injection molding landscape is rapidly evolving, driven by automation and the integration of smart technologies. An advanced guide would explore the role of automation in improving efficiency, reducing labor costs, and increasing consistency. This would include discussions on robotic handling systems, automated quality inspection systems, and the integration of data acquisition systems into a centralized control system.
Furthermore, the guide would likely incorporate a discussion on the application of advanced technologies such as machine learning and artificial intelligence. These technologies offer the potential for predictive maintenance, process optimization through real-time data analysis, and the development of self-learning control systems that continuously adapt to changing conditions, pushing the boundaries of efficiency and quality in injection molding.
In conclusion, an *Advanced Moulding Injection Process Optimization Guide* serves as a vital resource for manufacturers seeking to enhance their injection molding operations. By integrating fundamental principles, advanced techniques, and a focus on automation and emerging technologies, such a guide empowers manufacturers to optimize their processes, improve product quality, reduce costs, and ultimately gain a competitive edge in the market.