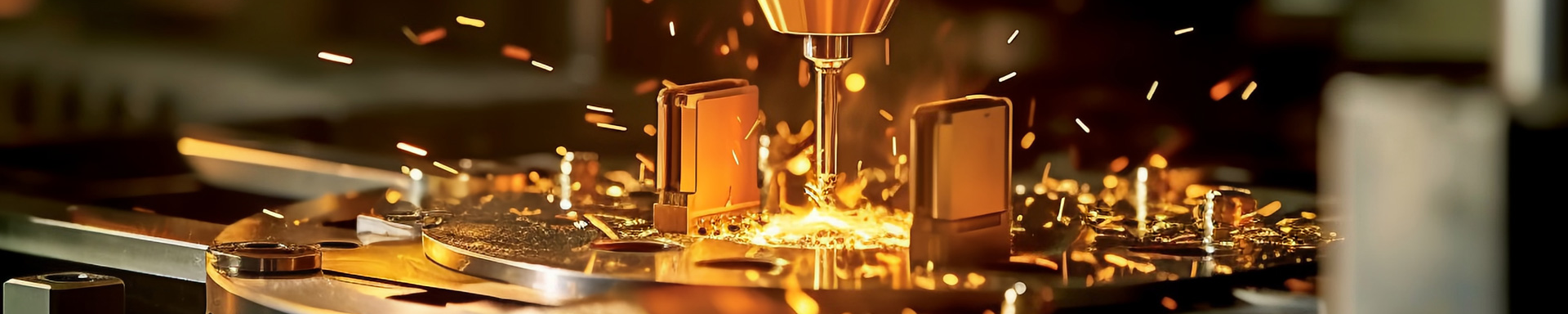
Explore the World of Precision Moulding Injection
2024-11-20 16:06Explore the world of precision molding injection is a journey into the heart of manufacturing, where intricate designs meet high-tech machinery to create parts with unparalleled accuracy and complexity. From the minuscule components within a smartphone to the robust structural elements of a car, precision molding injection shapes our modern world. Understanding this process reveals a fascinating interplay of engineering, materials science, and manufacturing expertise. This exploration delves into the intricacies of this technique, illuminating its capabilities and applications in diverse industries.
The Fundamentals of Precision Molding Injection
Precision molding injection, a subset of injection molding, focuses on producing parts with extremely tight tolerances and exceptional surface finishes. Unlike standard injection molding, which allows for some degree of dimensional variation, precision molding demands exacting control over every aspect of the process, from the temperature and pressure of the molten material to the precise movement of the mold itself. This necessitates advanced machinery and meticulous monitoring throughout the entire production cycle. The result is a component that meets stringent quality standards, often exceeding the requirements of conventional manufacturing methods.
The core of the process involves injecting molten thermoplastic or thermoset polymer into a precisely engineered mold cavity. The mold, typically crafted from hardened steel or other high-performance materials, is designed to replicate the exact shape and dimensions of the desired part. The molten plastic is forced into the cavity under high pressure, filling every detail of the mold. Once the plastic cools and solidifies, the mold opens, and the finished part is ejected. The entire process is highly automated, ensuring consistency and repeatability.
Materials and Mold Design: The Building Blocks of Precision
The choice of material is critical in achieving precision. Different polymers offer distinct properties, such as strength, flexibility, heat resistance, and chemical resistance. Selecting the optimal material is a crucial step in ensuring the final product meets its intended application requirements. This selection often involves considering factors like the part's function, environmental conditions, and desired lifespan.
Mold design plays an equally significant role. Precision molding demands molds crafted to incredibly tight tolerances, often involving intricate features, undercuts, and complex geometries. Computer-aided design (CAD) and computer-aided manufacturing (CAM) are indispensable tools in this stage, enabling engineers to create highly detailed and accurate mold designs. Sophisticated software simulates the injection process, helping to optimize the mold design and predict potential problems before production begins. The material used for the mold itself must be durable enough to withstand the high pressures and temperatures involved, and possess the dimensional stability necessary to maintain precision over many cycles.
Quality Control and Assurance: Ensuring Perfection
Precision molding injection demands rigorous quality control throughout the entire process. Regular inspections and measurements are conducted at each stage, ensuring that the materials meet specifications and the machinery is functioning optimally. Statistical process control (SPC) techniques are employed to monitor and analyze process variations, identifying and addressing potential problems before they affect the quality of the finished parts.
Advanced measuring equipment, such as coordinate measuring machines (CMMs) and laser scanners, are used to verify the dimensions and surface finish of the molded parts. These tools provide highly accurate measurements, allowing for precise identification of any deviations from the design specifications. Moreover, non-destructive testing methods, such as X-ray inspection, may be employed to detect internal flaws or inconsistencies. This meticulous approach to quality assurance is essential for delivering parts that meet the demanding standards of precision applications.
Applications Across Industries: A Wide Range of Possibilities
The capabilities of precision molding injection extend across a vast range of industries. In the medical device industry, it's used to create intricate components for implants, prosthetics, and diagnostic tools, requiring exceptional accuracy and biocompatibility. The automotive industry utilizes precision molding for fuel injection systems, sensors, and other crucial parts where precise dimensions and tolerances are paramount for optimal performance and safety.
Electronics manufacturing relies heavily on precision molding for the creation of connectors, housings, and other components. The aerospace industry also benefits from this technology, producing lightweight yet durable parts for aircraft and spacecraft. Even in consumer goods, precision molding is used to create high-quality, aesthetically pleasing components for electronics, appliances, and other products. The versatility and precision of this manufacturing technique make it an indispensable tool in shaping the world around us.
The Future of Precision Molding Injection: Innovation and Advancement
The field of precision molding injection is constantly evolving, driven by advancements in materials science, automation, and manufacturing technology. New polymers with enhanced properties are constantly being developed, expanding the range of applications for this technique. The integration of robotics and artificial intelligence (AI) is improving automation, leading to increased efficiency and improved part consistency.
Additive manufacturing techniques are also being integrated with traditional molding processes, offering the potential for creating even more complex and intricate parts. As technology continues to advance, precision molding injection will undoubtedly play an increasingly important role in the manufacturing of high-precision components across various industries, continuing to shape the future of innovative design and production.