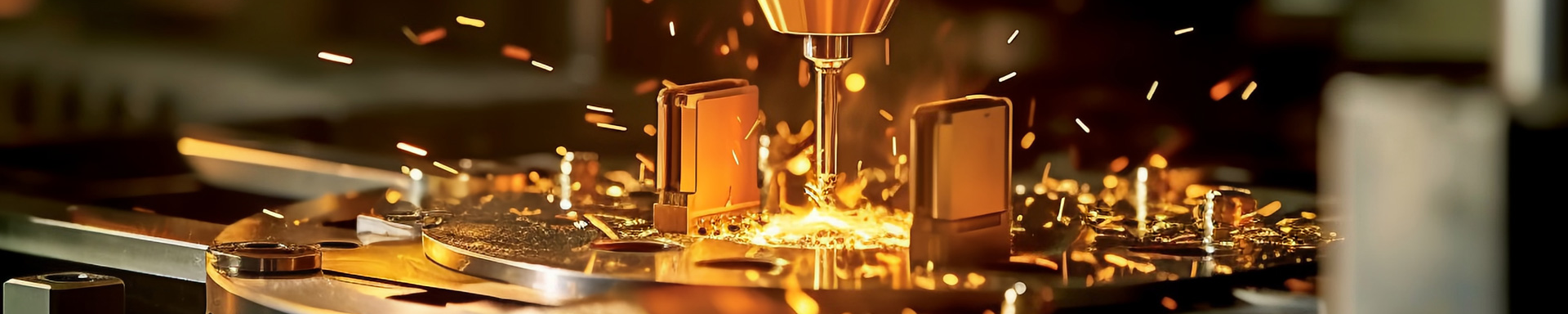
Advanced Progressive Die Strip Layout Strategies
2025-01-03 15:49Minimizing Waste Through Optimized Nesting
Traditional progressive die strip layouts often focused on simple nesting algorithms, aiming for the most straightforward arrangement of parts within the strip. Advanced strategies, however, utilize sophisticated software and algorithms to achieve far greater optimization. These tools consider factors beyond simply fitting parts together. They analyze the specific geometry of the part, including features like curves, holes, and intricate details, to minimize material waste. This often involves the use of algorithms that explore multiple possible layouts, evaluating each for waste and efficiency before selecting the optimal solution. The reduction in material waste translates directly into lower material costs and a smaller environmental footprint.
Furthermore, advanced nesting algorithms can handle various strip widths and lengths, dynamically adjusting the layout to maximize yield. This adaptability is crucial when dealing with different material specifications or order quantities. The ability to automatically generate different layouts based on these variable parameters significantly increases flexibility and responsiveness within the manufacturing process.
Incorporating Blanking and Piercing Operations
The efficient sequencing of blanking and piercing operations within the progressive die is another critical aspect of advanced strip layout. Simply arranging the parts isn\'t enough; the order of operations must be carefully planned to minimize the stress on the material and the die itself. Poor sequencing can lead to warping, breakage, or increased wear and tear on the die components, requiring more frequent and costly maintenance.
Advanced strategies use simulations to predict the stresses induced during each step of the stamping process. This allows designers to optimize the order of operations to reduce material deformation and improve the overall quality of the stamped parts. The software often incorporates finite element analysis (FEA) to model the material behavior under various loading conditions, providing detailed insights into potential issues before the die is even built. This predictive capability is crucial for preventing costly rework and delays.
Addressing Complex Part Geometries and Features
Many modern parts exhibit intricate geometries and complex features that pose significant challenges for traditional strip layout methods. These parts often require a more sophisticated approach that considers the interaction between adjacent parts and the overall flow of material through the die. Advanced techniques address these challenges by employing algorithms that specifically handle these complexities.
For instance, strategies such as \"virtual prototyping\" allow designers to virtually assemble the die and simulate the stamping process, identifying potential issues early on. This avoids costly and time-consuming trial-and-error approaches. The software can simulate the bending and forming of the material, accurately predicting the final part shape and identifying potential problems such as wrinkles, cracks, or insufficient material for certain features. The early detection and correction of these problems are essential for maximizing yield and producing high-quality parts.
Utilizing Advanced Software and Automation
The implementation of advanced progressive die strip layout strategies heavily relies on sophisticated software and automation. These tools provide the necessary computational power to evaluate numerous layout possibilities and optimize them based on various criteria, such as material waste, production time, and die complexity. Manual layout methods simply cannot achieve the same level of optimization and efficiency.
Furthermore, the integration of these software tools into a broader manufacturing execution system (MES) allows for seamless data exchange and automated production planning. This facilitates real-time tracking of material usage, production progress, and potential bottlenecks, enabling proactive adjustments to maintain optimal efficiency. The automation aspect minimizes human error, ensuring consistent and high-quality results across multiple production runs.
Considering Tolerance and Variability
Advanced strategies also account for the inherent variability in materials and manufacturing processes. Parts are rarely produced with perfect precision, and tolerances must be considered in the layout design. This is particularly important for parts with tight tolerances or those requiring precise alignment with other components.
Advanced software includes features that account for material variations and process tolerances. The algorithms consider these uncertainties when determining the optimal layout, ensuring that the resulting design is robust enough to handle these inevitable variations. This proactive approach helps prevent rejected parts due to dimensional inaccuracies, saving both time and resources.