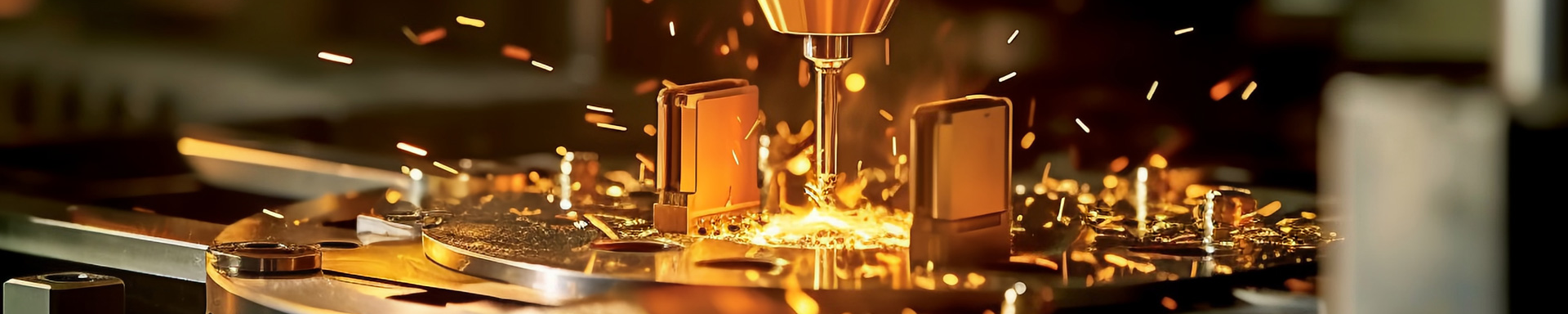
Advanced Punching and Shearing Die Design Techniques
2025-01-08 14:20Material Selection and Properties
The selection of appropriate materials for punches and dies is paramount. The die material must possess exceptional hardness, wear resistance, and toughness to withstand the repetitive stresses and abrasive forces during operation. Common choices include tool steels like high-speed steel (HSS), powder metallurgy (PM) tool steels, and carbide materials. The choice hinges on factors like the material being processed (e.g., aluminum, stainless steel, titanium), the desired die life, and the production volume. High-speed steels offer a good balance of properties and cost-effectiveness for many applications. However, for extremely high production runs or materials with high abrasive properties, carbide materials offer superior wear resistance, justifying their higher initial cost.
Furthermore, understanding the mechanical properties of the material being punched or sheared is crucial. Yield strength, tensile strength, and ductility directly influence the die design. Materials with high yield strengths require greater force to deform, demanding robust die construction. Ductility affects the burr formation during shearing, influencing the need for specialized die designs to minimize burr size and improve surface finish.
Progressive Die Design
Progressive dies represent a significant advancement in punching and shearing technology, enabling multiple operations to be performed in a single pass of the workpiece. This significantly boosts production efficiency by eliminating the need for multiple individual dies and reducing handling time. These dies incorporate a series of stations, each performing a specific operation such as punching, blanking, forming, or embossing. The workpiece is progressively fed through these stations, undergoing a sequence of transformations before exiting as a finished part.
Designing effective progressive dies demands careful planning and precise tooling. The accurate alignment of stations is critical to prevent misalignment and part defects. Tooling design must account for material flow, clearances, and potential springback effects to ensure accurate part dimensions. Finite element analysis (FEA) is often employed in the design process to simulate the stresses and deformations involved, enabling optimization of the die geometry and minimizing potential issues.
Advanced Shearing Techniques
Shearing operations, critical for separating sheet metal parts, benefit from advanced techniques to enhance precision and reduce defects. Methods such as precision blanking utilize specialized dies with accurately controlled cutting edges to achieve exceptionally smooth cuts and minimize burr formation. This requires tight tolerances in die construction and precise control of the shearing process.
Other advanced shearing techniques focus on mitigating issues like shear fracture, which can result in uneven cuts and surface imperfections. This includes optimizing the shear angle, using specialized die geometries, and incorporating features like nibblers to facilitate controlled material separation. Innovative designs often incorporate features that reduce the impact force during shearing, improving die life and minimizing noise and vibration.
Computer-Aided Design (CAD) and Simulation
Modern die design relies heavily on Computer-Aided Design (CAD) software. CAD facilitates the creation of detailed three-dimensional models of dies, enabling comprehensive visualization and analysis. This allows designers to identify potential design flaws, optimize geometry, and simulate the manufacturing process before actual die construction, saving time and resources.
Furthermore, simulation techniques, including FEA, play a crucial role in verifying the design's functionality and predicting its performance. FEA allows designers to analyze stress distributions, predict deformation patterns, and assess the potential for failure under various operating conditions. This predictive capability enables the optimization of die design for durability, efficiency, and cost-effectiveness.
Die Maintenance and Optimization
Even with advanced design techniques, proper die maintenance is crucial for maximizing die life and preventing costly downtime. Regular inspection, sharpening, and lubrication are essential to prevent wear and tear. Wear monitoring systems can help detect early signs of damage, enabling proactive maintenance and extending the die's lifespan.
Continuous optimization of die design and manufacturing processes is essential for improving efficiency and reducing costs. Data analysis of production parameters, such as die life, part quality, and production rates, can inform design improvements and process adjustments, leading to better overall performance. This iterative process of design, simulation, testing, and optimization is fundamental to achieving excellence in advanced punching and shearing die design.