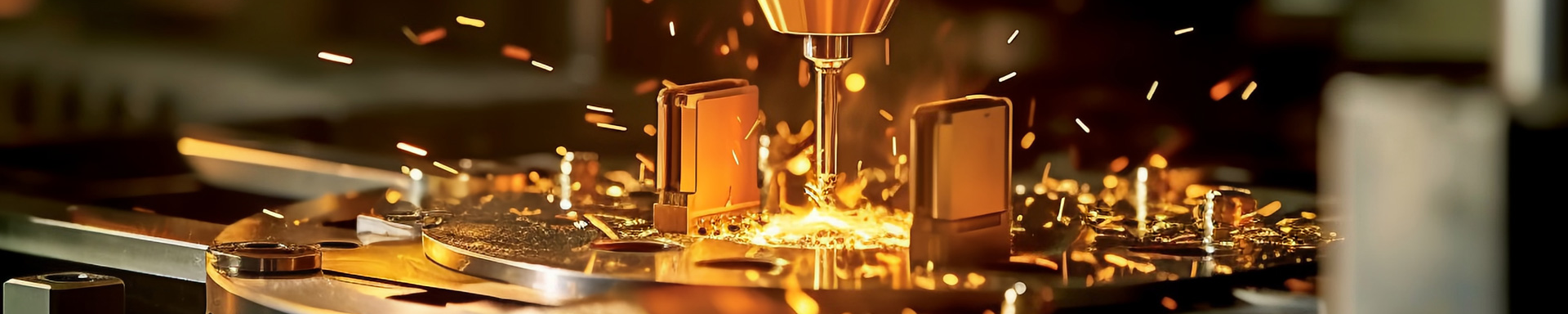
Innovative Solutions for Punching and Shearing Dies
2025-01-08 14:18Material Advancements: Beyond Traditional Steels
For decades, tool steels like high-speed steel (HSS) and various grades of high-carbon tool steel dominated the punching and shearing die market. However, the limitations of these materials in terms of wear resistance, toughness, and overall lifespan have spurred the adoption of advanced materials. Tungsten carbide, for instance, offers significantly improved wear resistance, allowing for longer tool life and reduced downtime. This translates directly to cost savings and increased production output. The use of carbide inserts, often brazed or mechanically clamped onto the die, provides a cost-effective way to leverage the superior properties of carbide while retaining the structural integrity of a steel body.
Beyond carbide, ceramic materials are emerging as a viable alternative for specific applications. Their exceptional hardness and wear resistance make them particularly suitable for processing highly abrasive materials or in high-speed punching operations. However, ceramics also present challenges related to brittleness and higher manufacturing costs, limiting their wider adoption. Ongoing research focuses on improving the toughness of ceramic dies and developing cost-effective manufacturing techniques to make them more competitive.
Furthermore, the development of advanced steel alloys with enhanced properties, such as increased hardness, improved toughness, and superior resistance to thermal fatigue, continues to offer incremental improvements in traditional die materials. These improvements subtly yet significantly enhance die performance and longevity, minimizing maintenance and replacement costs.
Geometric Innovations: Optimized Designs for Enhanced Performance
The geometry of punching and shearing dies significantly impacts their performance, particularly in terms of cutting force, burr formation, and overall part quality. Traditional designs often relied on simple geometries, leading to suboptimal results. Recent advancements focus on optimizing die geometries using advanced simulation techniques and computational fluid dynamics (CFD) modeling.
These simulations allow engineers to predict and minimize the stresses experienced by the die during operation, leading to the design of dies with improved strength and fatigue resistance. Moreover, simulations aid in optimizing the cutting geometry to reduce burr formation, improve surface finish, and minimize material deformation. This results in higher-quality parts that require less secondary finishing, reducing overall manufacturing costs.
The incorporation of advanced features, such as profiled punches and shear angles, contributes significantly to improving cutting performance. By carefully controlling the shear angle, the stress concentration during the cutting process can be reduced, minimizing the risk of die breakage and improving the surface finish of the punched parts. Similarly, profiled punches can help to control the direction of material flow during cutting, reducing burr formation and improving part accuracy.
Manufacturing Processes: Precision and Efficiency in Die Production
The manufacturing processes used to create punching and shearing dies directly impact their quality, precision, and overall cost. Traditional methods relied heavily on manual machining and grinding, a process that is both time-consuming and susceptible to human error. Recent years have witnessed the adoption of advanced manufacturing techniques like wire EDM (Electrical Discharge Machining), laser cutting, and 3D printing.
Wire EDM allows for the creation of extremely intricate die geometries with exceptional precision, enabling the manufacture of dies with complex features that would be impossible to achieve using traditional methods. Laser cutting offers high speed and accuracy for simpler die components, reducing manufacturing lead times. 3D printing, while still in its relatively early stages of adoption for large-scale die production, offers the potential to create complex, customized dies with reduced material waste and lead times.
The integration of Computer Numerical Control (CNC) machining continues to enhance the accuracy and efficiency of die manufacturing. CNC machining allows for the precise control of cutting parameters, resulting in dies with superior dimensional accuracy and surface finish. Furthermore, CNC machining can be easily programmed to automate repetitive tasks, reducing manufacturing time and labor costs.
Smart Dies and Industry 4.0 Integration
The integration of sensors and data analytics into punching and shearing dies is transforming the way these tools are used and maintained. Smart dies incorporate sensors to monitor key parameters such as cutting force, die temperature, and vibration. This data can be used to predict potential failures, optimize cutting parameters, and improve overall process efficiency.
Furthermore, the integration of smart dies with existing manufacturing execution systems (MES) enables real-time monitoring and control of the punching and shearing process. This facilitates predictive maintenance, reducing downtime and improving overall equipment effectiveness (OEE). Data collected from smart dies can also be analyzed to identify trends and optimize the entire manufacturing process, resulting in significant improvements in quality, efficiency, and productivity.
The adoption of Industry 4.0 principles, including digital twins and machine learning, promises further advancements in the design, manufacturing, and operation of punching and shearing dies. Digital twins allow for virtual testing and optimization of die designs before physical prototypes are produced, significantly reducing development time and costs. Machine learning algorithms can be used to analyze vast amounts of data collected from smart dies, leading to improvements in predictive maintenance, process optimization, and overall manufacturing performance.