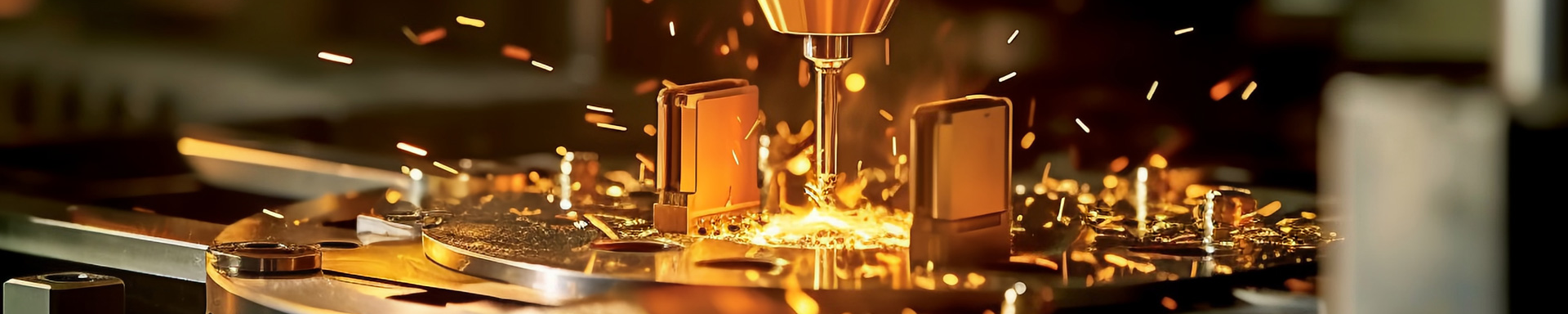
Cost Effective Punching and Shearing Die Solutions
2025-01-08 14:11Material Selection for Cost Optimization
The choice of material for your punching and shearing dies significantly impacts both their lifespan and initial cost. While high-speed tool steels offer exceptional durability and longevity, their price point can be considerably higher. Alternatively, materials like carbide, powder metallurgy high-speed steel, and even certain hardened tool steels represent viable alternatives offering a more favorable cost-performance ratio. The selection process must carefully weigh the material’s hardness, wear resistance, and toughness against the expected production volume and the nature of the material being processed. A thorough analysis of the material’s properties in relation to the specific application is crucial to avoid premature wear and costly replacements.
Furthermore, exploring less conventional materials or innovative composite materials can sometimes yield unexpected cost savings. These materials may require more extensive research and development, but the potential for long-term cost reduction might justify the initial investment. Consider the total cost of ownership (TCO), which encompasses not just the initial purchase price but also factors such as maintenance, repair, and replacement costs over the die's operational lifespan. Choosing a material with a longer service life might seem more expensive upfront but can significantly reduce overall costs in the long run.
Die Design and Manufacturing Techniques
Strategic die design is another crucial element in achieving cost effectiveness. Simple, robust designs often prove more cost-efficient than complex, intricate ones. Avoid unnecessary features or complexities that don't directly contribute to the desired punching or shearing outcome. Computer-aided design (CAD) and computer-aided manufacturing (CAM) software can significantly aid in optimizing die designs for cost-effectiveness, allowing for precise simulations and the detection of potential weaknesses before manufacturing even begins. This predictive analysis minimizes the risk of costly errors and rework.
The manufacturing process itself also plays a significant role. Methods like wire electrical discharge machining (EDM) allow for intricate designs and high precision, but they can be relatively expensive. Alternatively, simpler methods like milling or grinding, while potentially resulting in less refined geometries, can be significantly more cost-effective, especially for high-volume production runs. Careful consideration of manufacturing tolerances is essential; tighter tolerances may enhance precision but also increase manufacturing costs. Finding the optimal balance between precision and cost is a key aspect of cost-effective die design and manufacturing.
Optimizing Die Life and Maintenance
Extending the lifespan of your punching and shearing dies is a direct path to cost reduction. Implementing proper lubrication techniques, using appropriate cutting fluids, and ensuring optimal machine settings are all crucial for minimizing wear and tear. Regular maintenance checks, including inspections for signs of wear, damage, or misalignment, are equally important. Proactive maintenance helps prevent catastrophic failures and costly downtime, ensuring the die remains productive for its intended lifespan.
Implementing a comprehensive maintenance program that includes preventative measures and regular inspections can significantly extend the die's life. This program should also incorporate a detailed tracking system to monitor die performance and identify potential issues early on. Careful attention to details like sharpening and regrinding can also revitalize worn dies, extending their usable life and delaying the need for complete replacement. A well-structured maintenance plan not only increases the lifespan of the dies but also minimizes unscheduled downtime, leading to significant cost savings.
Outsourcing and Collaboration
Outsourcing die manufacturing to specialized companies can sometimes offer significant cost advantages. These companies often possess advanced equipment, expertise, and economies of scale that can result in lower production costs and faster turnaround times. Collaborating with experienced die manufacturers allows for valuable input during the design phase, ensuring the die is optimized for both performance and cost-effectiveness.
Furthermore, forging strong relationships with suppliers can lead to access to preferred pricing, timely delivery, and potential technical support. This collaborative approach extends beyond simply purchasing dies; it fosters a partnership that contributes to a more efficient and cost-effective overall production process. A well-chosen supplier can act as a valuable resource, offering insights and advice that can significantly impact your bottom line.
Analyzing Total Cost of Ownership (TCO)
Finally, it's crucial to consider the total cost of ownership (TCO) when evaluating different die solutions. TCO encompasses not only the initial investment but also all subsequent costs associated with the die, including maintenance, repairs, replacements, and downtime. A comprehensive TCO analysis allows for a more informed decision, ensuring that the chosen solution delivers the optimal balance between upfront costs and long-term operational expenses.
By carefully considering all aspects of the die's lifecycle, from material selection and design to manufacturing, maintenance, and eventual replacement, businesses can make well-informed decisions that lead to significant cost savings without compromising quality or performance. A holistic approach to cost-effectiveness ensures that punching and shearing dies contribute positively to the overall profitability and competitiveness of the manufacturing process.