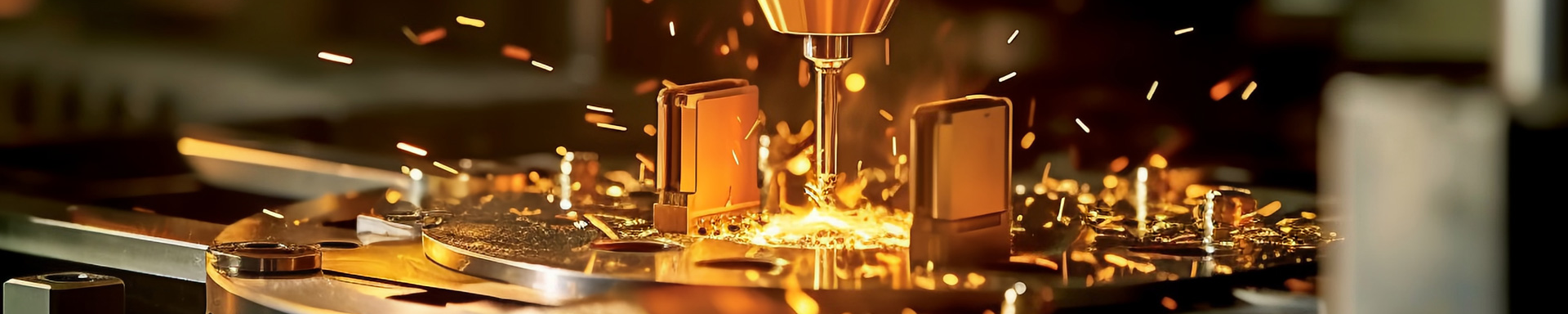
High Quality Moulding Injection solutions Explained
2024-11-20 16:02High-quality molding injection is a cornerstone of modern manufacturing, enabling the mass production of intricate and precise parts across a vast range of industries. From the tiny components within your smartphone to the robust casings of automotive engines, injection molding's versatility and efficiency are unmatched. But what exactly constitutes a "high-quality" injection molding solution? This goes beyond simply creating a functional part; it encompasses a multifaceted process demanding precision, expertise, and a commitment to excellence at every stage. This exploration delves into the crucial aspects that define superior injection molding solutions.
Material Selection: The Foundation of Quality
The journey towards high-quality injection molding begins with the selection of the appropriate raw material. This choice is dictated by the intended application of the final product, demanding a thorough understanding of the material's properties. Factors such as strength, durability, flexibility, heat resistance, chemical resistance, and aesthetic considerations all play a pivotal role. Will the part need to withstand extreme temperatures? Will it be exposed to harsh chemicals? Will it require a specific surface finish? These questions must be answered before selecting a material, which might range from common thermoplastics like polypropylene or ABS to more specialized engineering plastics like PEEK or nylon. The proper selection ensures the final product meets or exceeds performance expectations.
Furthermore, sourcing materials from reputable suppliers is critical. Consistent material quality is paramount; variations in the raw material can lead to inconsistencies in the finished product, potentially causing defects or compromising its performance. Reputable suppliers provide certifications and documentation to guarantee the quality and consistency of their materials, further enhancing the overall quality control of the injection molding process.
Precision Mold Design and Manufacturing: The Blueprint for Success
The mold itself is the heart of the injection molding process. High-quality injection molding necessitates a meticulously designed and manufactured mold. This requires advanced CAD/CAM software and experienced mold makers who understand the nuances of mold design and the potential for defects. The mold's design must consider factors such as gate placement, cooling channels, and ejection mechanisms to ensure efficient and defect-free part production. Improper design can lead to sink marks, warping, or incomplete filling of the mold cavity.
Precision in mold manufacturing is equally crucial. Even minor imperfections in the mold can lead to significant defects in the final product. Advanced machining techniques and rigorous quality control checks are necessary to ensure the mold's dimensional accuracy and surface finish. The use of high-quality mold steel also contributes significantly to the mold's longevity and the consistency of the parts produced.
Process Optimization and Control: Ensuring Consistent Quality
Once the mold is ready, the injection molding process itself must be carefully controlled and optimized. Parameters such as injection pressure, injection speed, melt temperature, mold temperature, and holding time all significantly influence the quality of the final product. These parameters must be precisely controlled and monitored to ensure consistent part quality and minimize defects. Advanced injection molding machines equipped with sophisticated control systems are essential for this precise control.
Continuous monitoring and data analysis are crucial aspects of process optimization. Regular inspection of the produced parts and analysis of process parameters allow for timely adjustments and prevent the production of defective parts. Statistical process control (SPC) techniques can be employed to identify and address potential issues before they lead to widespread defects. This proactive approach ensures consistent, high-quality output.
Quality Control and Inspection: Guaranteeing Perfection
Rigorous quality control is a non-negotiable aspect of high-quality injection molding. Comprehensive inspection procedures must be in place to detect and eliminate defects at various stages of the process, from raw material inspection to the final product verification. This might involve visual inspection, dimensional measurement, and advanced testing methods like X-ray inspection or destructive testing.
Implementing a robust quality management system, such as ISO 9001, is vital for ensuring consistent quality and traceability throughout the entire process. Documentation of all processes, materials, and inspections is crucial for identifying and rectifying any issues that may arise and maintaining a high level of quality and accountability.
In conclusion, achieving high-quality injection molding solutions requires a holistic approach encompassing meticulous material selection, precision mold design and manufacturing, optimized process control, and rigorous quality inspection. By prioritizing these crucial aspects, manufacturers can ensure the consistent production of high-quality, reliable parts that meet or exceed customer expectations.