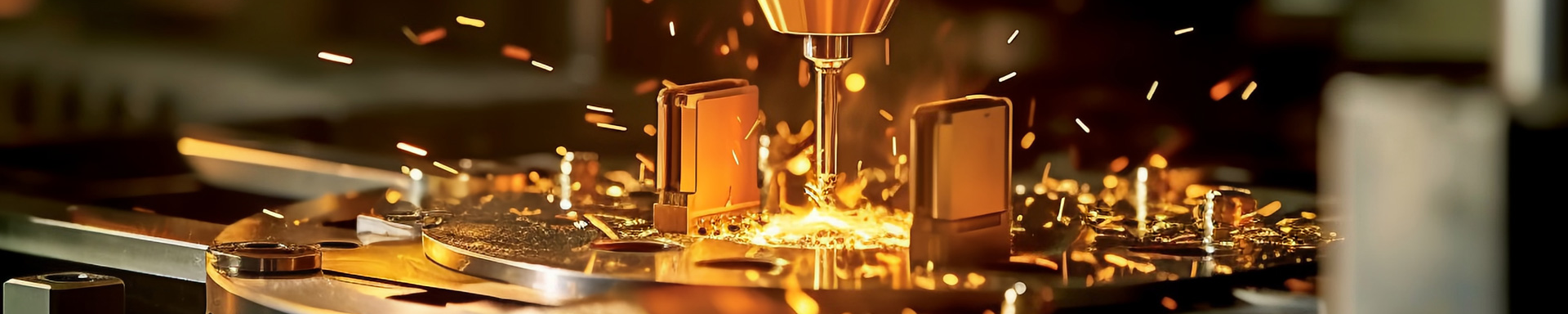
High Precision Punching and Shearing Die Manufacturing
2025-01-08 14:17Material Selection: The Foundation of Precision
The choice of materials for high-precision dies directly impacts their performance and longevity. Tool steels, renowned for their exceptional hardness, wear resistance, and toughness, are the cornerstone of this manufacturing process. Different grades of tool steel are selected based on the specific application, material being processed, and desired die life. Factors like carbon content, alloying elements (chromium, vanadium, molybdenum), and heat treatment processes all play crucial roles in determining the final properties of the die. Proper material selection is paramount in ensuring consistent and accurate punching and shearing operations, minimizing wear, and maximizing the lifespan of the die.
Beyond tool steels, other materials such as carbide and cermet are employed for specific applications demanding even greater wear resistance or improved performance with difficult-to-machine materials. The selection process involves careful consideration of factors like the material's yield strength, tensile strength, hardness, and its response to various heat treatments. Advanced characterization techniques, including microscopic analysis and hardness testing, are used to verify the quality and consistency of the chosen materials before die manufacturing commences.
Design and Engineering: Achieving Dimensional Accuracy
The design phase is crucial for achieving the desired precision in punching and shearing dies. Sophisticated Computer-Aided Design (CAD) software is employed to create intricate 3D models of the dies, allowing for precise control over every dimension and feature. Finite Element Analysis (FEA) is often incorporated into the design process to simulate the stresses and strains experienced by the die during operation, enabling engineers to optimize the design for maximum durability and performance. This predictive modeling minimizes the risk of die failure and ensures the consistent production of high-quality parts.
Tolerance specifications are rigorously defined during the design phase, reflecting the required precision of the final product. These tolerances, often measured in micrometers, demand meticulous attention to detail throughout the manufacturing process. The design also considers factors such as clearance between the punch and die, the geometry of the shearing edges, and the overall die structure to optimize cutting efficiency and prevent deformation or damage to the workpiece.
Manufacturing Processes: Precision Machining and Finishing
The manufacturing process for high-precision punching and shearing dies employs advanced machining techniques, including wire Electrical Discharge Machining (EDM), sinker EDM, and ultra-precision milling. Wire EDM offers exceptional accuracy for intricate shapes and complex geometries, while sinker EDM excels in creating precise cavities and intricate details. Ultra-precision milling utilizes specialized machines with high-speed spindles and advanced control systems, enabling the creation of extremely smooth and accurate surfaces.
After machining, the dies undergo rigorous finishing processes to achieve the desired surface quality and dimensional accuracy. These processes include grinding, lapping, honing, and polishing, each contributing to the overall precision of the die. Electrochemical polishing is often employed to create a mirror-like finish, minimizing friction and improving the lifespan of the die. Regular quality checks and inspections are implemented throughout the manufacturing process to ensure adherence to stringent tolerance requirements.
Quality Control and Inspection: Ensuring Dimensional Accuracy and Performance
Rigorous quality control and inspection procedures are essential to ensure that the manufactured dies meet the specified tolerances and performance requirements. Dimensional metrology techniques, employing coordinate measuring machines (CMMs) and laser scanning systems, are used to verify the accuracy of the die's dimensions and geometry. Surface roughness measurements are performed to assess the surface finish, ensuring optimal performance and minimizing friction during operation.
Beyond dimensional accuracy, the die's functionality is also rigorously tested. Trial runs are conducted to evaluate the die's cutting performance, ensuring consistent part quality and minimizing defects. These tests also assess the die's durability and longevity under typical operating conditions. Data collected from these tests is crucial in evaluating the die's performance, identifying potential areas for improvement, and optimizing the manufacturing process for future productions.
Conclusion: The Pursuit of Perfection
High-precision punching and shearing die manufacturing is a testament to the advancements in engineering and manufacturing technology. The combination of advanced materials, sophisticated design techniques, precision machining processes, and stringent quality control measures enables the production of dies capable of creating components with exceptional accuracy. The pursuit of ever-higher precision in die manufacturing is driven by the demand for increasingly sophisticated and complex components in diverse industries, pushing the boundaries of what is possible and contributing to innovations across numerous sectors.