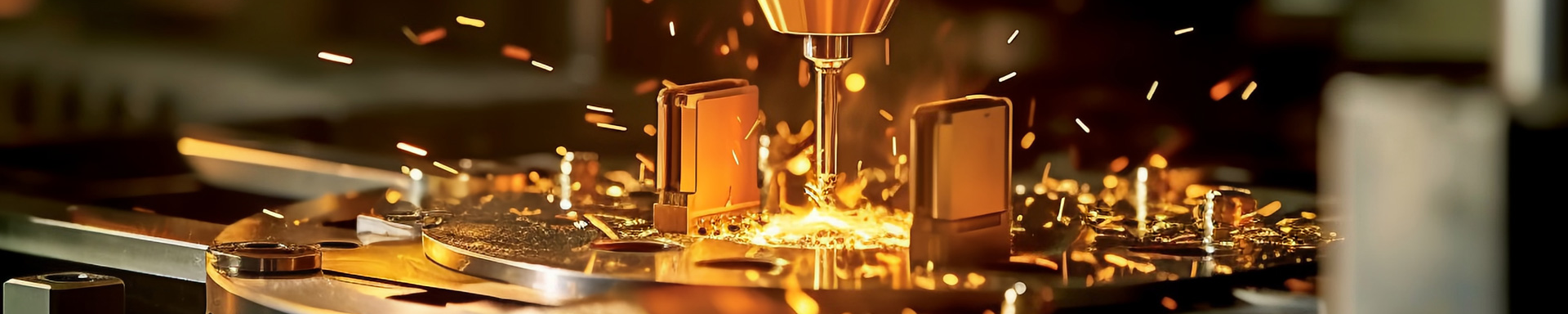
Optimizing Performance of Punching and Shearing Dies
2025-01-08 14:16Material Selection for Optimal Performance
The selection of appropriate materials for both the punch and die components is paramount. The materials must possess sufficient hardness and wear resistance to withstand the repetitive stresses of punching and shearing. Tool steels, such as high-speed steel (HSS) and various powder metallurgical (PM) tool steels, are commonly employed due to their excellent properties. The choice depends on factors like the material being processed, the required die life, and the production volume. For instance, processing harder materials necessitates utilizing tougher and more wear-resistant tool steels. Furthermore, the selection should consider factors like the cost-effectiveness of the material and its availability.
In addition to the die materials, the properties of the sheet metal being processed significantly influence die performance. The metal's tensile strength, ductility, and surface finish affect the cutting forces, tool wear, and the quality of the finished product. Understanding the material's characteristics is crucial for selecting appropriate die designs and operating parameters. For example, a material with high tensile strength will require a more robust die design and potentially higher cutting forces, leading to increased wear and tear if not properly managed.
Die Design Considerations for Enhanced Efficiency
The geometry and design of the punch and die play a crucial role in determining their performance. Several critical aspects must be considered during the design phase. Firstly, the sharpness of the cutting edges is essential for minimizing cutting forces and reducing wear. A well-designed die will have precisely honed cutting edges that ensure a clean and accurate cut. Regular sharpening and maintenance of these edges are vital to maintaining optimal performance. Blunt edges lead to increased friction, burr formation, and premature tool failure.
Secondly, the clearance between the punch and die is a critical parameter. This clearance must be carefully controlled to ensure efficient shearing. Excessive clearance can result in a ragged cut and increased burr formation, while insufficient clearance may lead to excessive friction and premature tool wear. The optimal clearance depends on factors such as the material thickness and the type of die being used. Careful consideration of this parameter during the design phase is essential for achieving high-quality cuts and prolonging die life.
Finally, the overall design of the die should incorporate features that promote efficient material flow and reduce stresses on the components. This may involve incorporating features such as relief angles, support structures, and optimized material distribution to minimize distortion and enhance durability. Finite element analysis (FEA) can be employed to simulate the stresses and strains within the die during operation, allowing for the optimization of the design for maximum performance and longevity.
Operational Practices for Maximizing Die Lifespan
Optimal operational practices are crucial for maximizing the lifespan and performance of punching and shearing dies. Proper lubrication is essential in reducing friction and wear. Choosing the right lubricant, based on the material being processed and the operating conditions, can significantly extend die life. Regular lubrication, especially during continuous operation, is vital to prevent premature wear and tear.
Maintaining proper operating speeds and forces is also crucial. Excessive speeds or forces can lead to increased wear and potential damage to the die. Careful monitoring of these parameters during operation is necessary to ensure optimal performance and prevent premature failure. Regular inspections for wear and tear, along with timely replacement or repair, are also crucial aspects of maintaining optimum performance.
Furthermore, proper handling and storage of the dies are vital. Correct storage can prevent damage and corrosion, extending the lifespan of the tools. Following best practices for handling and storage, including the use of protective coatings or covers, will prevent damage to the cutting edges and improve longevity.
Advanced Techniques for Performance Optimization
In recent years, advancements in materials science and manufacturing techniques have led to significant improvements in punching and shearing die performance. The use of advanced materials, such as ceramic coatings or composite materials, can further enhance wear resistance and extend die life. These coatings can reduce friction, increase hardness, and improve heat dissipation, leading to enhanced performance and reduced wear.
Precision manufacturing techniques such as electrical discharge machining (EDM) and laser cutting allow for the creation of extremely accurate and complex die geometries. These techniques can improve the precision of the cutting edges and allow for the incorporation of sophisticated design features that optimize performance. The use of these advanced manufacturing techniques enables the creation of dies with enhanced precision, durability, and longevity.
By carefully considering material selection, die design, operational practices, and utilizing advanced technologies, manufacturers can significantly optimize the performance of punching and shearing dies. This leads to improved productivity, reduced downtime, lower manufacturing costs, and the production of higher-quality finished products. Continuous improvement and a commitment to best practices are essential for maintaining a competitive edge in the sheet metal fabrication industry.