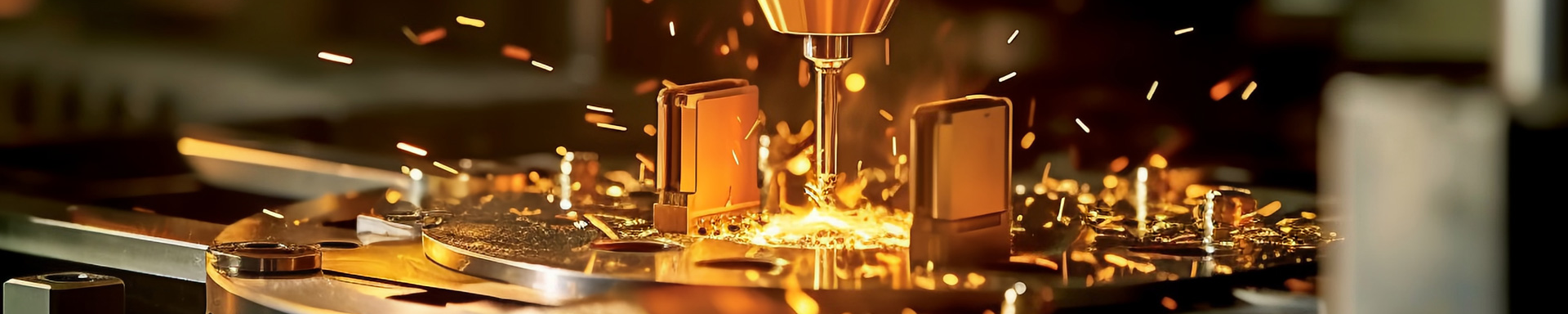
The Latest in Punching and Shearing Die Technology
2025-01-08 14:15Advanced Materials for Enhanced Durability and Performance
Traditional punching and shearing dies were often constructed from tool steels, known for their hardness and wear resistance. However, the demands of modern manufacturing, involving increasingly tougher materials and higher production speeds, have pushed the boundaries of these traditional materials. The latest advancements are focused on integrating advanced materials to improve the longevity and performance of these crucial tools. This includes the widespread adoption of high-speed steels (HSS), powder metallurgy tool steels, and even advanced ceramic materials for specific applications. These materials offer superior hardness, wear resistance, and toughness compared to their predecessors, leading to longer tool life and reduced downtime. This translates to significant cost savings for manufacturers in the long run, as die replacement and maintenance become less frequent.
Beyond the material itself, improvements in the heat treatment processes further enhance die performance. Precise control over heating and cooling cycles allows for the creation of dies with optimized microstructure, resulting in superior hardness, toughness, and resistance to cracking. These advancements extend the lifespan of the dies significantly and contribute to more consistent and predictable results throughout the production process. Furthermore, the use of coatings, such as titanium nitride (TiN) or diamond-like carbon (DLC), adds an extra layer of protection against wear and corrosion, maximizing the die's operating life even under harsh conditions.
Precision Engineering and Design Optimization
The precision of punching and shearing dies is paramount to producing high-quality parts. Modern advancements in Computer-Aided Design (CAD) and Computer-Aided Manufacturing (CAM) have revolutionized the design and manufacturing processes of these dies. Sophisticated CAD software allows engineers to simulate the die’s performance under various conditions, identifying potential weaknesses and optimizing the design for maximum efficiency and accuracy. This predictive modeling eliminates the need for extensive trial and error, significantly reducing development time and costs. Furthermore, it allows for the creation of complex geometries and intricate shapes that were previously impossible to achieve.
Additive manufacturing, also known as 3D printing, is emerging as a powerful tool in die creation. This technology allows for the rapid prototyping and production of complex die components, accelerating the development process and facilitating the creation of customized solutions tailored to specific needs. 3D printing enables the fabrication of dies with intricate internal channels for cooling, improving their thermal management and increasing their lifespan under high-stress conditions. The ability to create customized designs allows manufacturers to optimize the die for their particular materials and applications, achieving higher precision and efficiency.
Automation and Smart Manufacturing Integration
The integration of automation and smart manufacturing technologies is transforming the punching and shearing die industry. Automated die changing systems, for example, dramatically reduce downtime during production runs by allowing for quick and efficient tool changes. This automated system minimizes the risk of human error, increases overall efficiency and ensures consistent quality throughout the manufacturing process. Data acquisition systems connected to the punching and shearing machines collect real-time data on die performance, including wear and tear, allowing for predictive maintenance scheduling. This proactive approach minimizes unexpected downtime and optimizes production schedules.
Sensors embedded within the dies themselves are becoming increasingly prevalent, providing real-time information on temperature, pressure, and other critical parameters. This data allows for real-time monitoring of die performance and early detection of potential problems. By leveraging this data through advanced analytics and machine learning algorithms, manufacturers can optimize the production process, predict potential failures, and extend the lifespan of their dies even further. This smart manufacturing approach fosters a proactive and efficient production environment, leading to improved quality and reduced costs.
New Cutting-Edge Techniques
Beyond material advancements and automation, the field of punching and shearing die technology is continuously exploring innovative cutting techniques to improve efficiency and accuracy. High-speed punching, for instance, allows for significantly faster production rates without compromising quality. This technology requires precisely engineered dies capable of withstanding the increased stress and wear. Furthermore, the use of laser cutting in conjunction with traditional punching and shearing techniques offers new possibilities for intricate designs and complex geometries. Laser cutting can be employed to create precise cuts and holes that would be difficult, if not impossible, to achieve with traditional methods.
The development of new die materials and designs is also paving the way for more efficient cutting strategies. Improved designs reduce friction and optimize material flow, leading to less energy consumption and reduced wear on the die. These innovations contribute to improved sustainability and economic advantages for manufacturers. The ongoing research and development in the field ensure that punching and shearing die technology will continue to advance, enabling manufacturers to produce high-quality parts with increased efficiency and cost-effectiveness in the years to come.