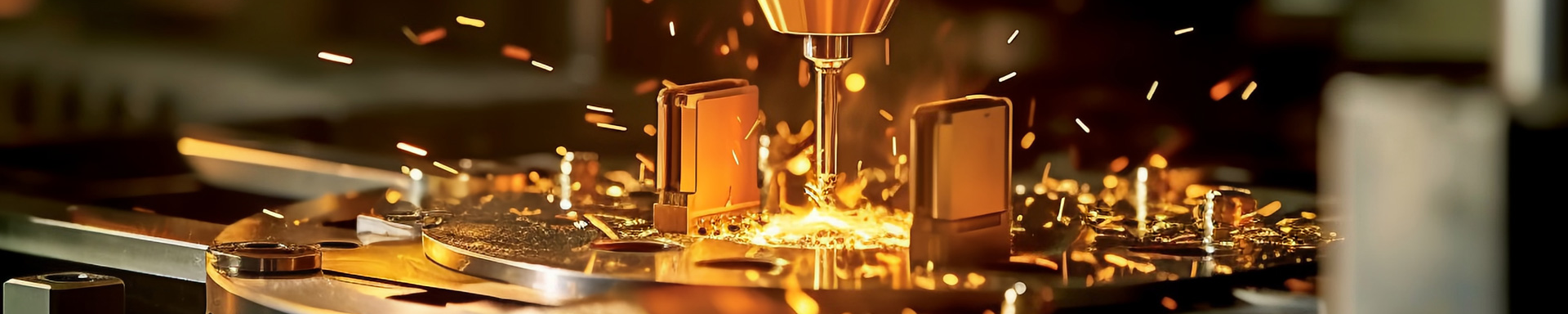
Optimizing Punching Stretching Mould Performance and Efficiency
2025-02-05 15:22Material Selection and its Impact
The choice of mold material fundamentally influences its lifespan, resistance to wear, and overall performance. High-strength tool steels, such as those alloyed with tungsten, molybdenum, and vanadium, are common choices due to their exceptional hardness and wear resistance. However, selecting the optimal steel grade requires careful consideration of the specific application. Factors like the material being formed (its tensile strength and ductility), the number of parts to be produced (defining the required tool life), and the forming forces involved all dictate the appropriate steel grade. Incorrect material selection can lead to premature tool failure, costly replacements, and production downtime.
Beyond the base material, surface treatments further enhance performance. Techniques like nitriding, hard chrome plating, and titanium nitride (TiN) coating significantly improve the surface hardness and resistance to abrasion and adhesion. These treatments create a protective layer that minimizes wear during the repeated punching and stretching cycles, extending the mold's useful life and reducing the need for frequent replacements or costly repairs. The selection of the appropriate surface treatment depends on factors such as the specific operating conditions, the desired level of wear resistance, and the budget allocated for mold maintenance.
Design Optimization for Enhanced Efficiency
The design of the punching and stretching mold directly impacts its performance and efficiency. Optimizing the design involves analyzing various aspects, including die geometry, punch design, and stripper plate configuration. A well-designed die, for instance, should minimize bending stresses in the workpiece, preventing premature fracture or failure. This often necessitates employing features like gradual radius transitions, strategically placed support structures, and optimized blank holding force.
The punch design also plays a critical role. Sharp, well-maintained punches are essential for clean, accurate cuts and to prevent burring or tearing of the material. The design should also incorporate features to minimize friction, such as lubrication grooves or coatings. Similarly, the stripper plate's design must efficiently remove the formed part from the punch without damaging the workpiece or the mold itself. Finite element analysis (FEA) simulations are increasingly used to predict stress and deformation patterns within the mold and workpiece during the forming process, enabling the design of more robust and efficient molds.
Process Parameter Control for Consistent Quality
Controlling the various process parameters is crucial for achieving consistent product quality and mold longevity. These parameters include the stamping force, the speed of the press, and the lubrication used. Precise control over stamping force prevents overworking the material, leading to cracking or tearing, and safeguards the mold from excessive stress. Similarly, appropriate press speed influences the forming process and the amount of wear on the tooling. Too high a speed can lead to increased wear and reduced tool life, while too low a speed can decrease production efficiency.
Lubrication is a critical factor in minimizing friction and wear between the workpiece and the mold components. The type and application method of the lubricant significantly impact the efficiency and lifespan of the mold. Proper lubrication reduces friction, improving surface finish and preventing galling or seizure. Regular monitoring and optimization of these process parameters are vital to maintaining consistent performance and extending the operational life of the mold.
Preventive Maintenance and Regular Inspection
A proactive approach to maintenance is vital for maximizing the performance and lifespan of punching and stretching molds. Regular inspection for wear, damage, or cracks is crucial in preventing catastrophic failures. Early detection of minor defects allows for timely repair or replacement, minimizing downtime and preventing costly rework. This involves visual inspection, dimensional checks, and potentially more sophisticated techniques like non-destructive testing (NDT) to assess the internal integrity of the mold.
Implementing a preventative maintenance schedule, incorporating lubrication, cleaning, and minor repairs, helps to extend the operational life of the mold. This schedule should include regular inspections, lubrication routines, and detailed documentation of any repairs or replacements made. Such a systematic approach minimizes unexpected breakdowns and ensures consistent production quality. Investing in preventive maintenance ultimately reduces long-term costs associated with unplanned downtime and frequent tool replacement.
By strategically addressing these aspects – material selection, design optimization, process parameter control, and preventative maintenance – manufacturers can significantly enhance the performance and efficiency of their punching and stretching molds, leading to increased productivity, improved product quality, and reduced manufacturing costs. The pursuit of optimization is an ongoing process requiring continuous monitoring, analysis, and adaptation to achieve optimal results.