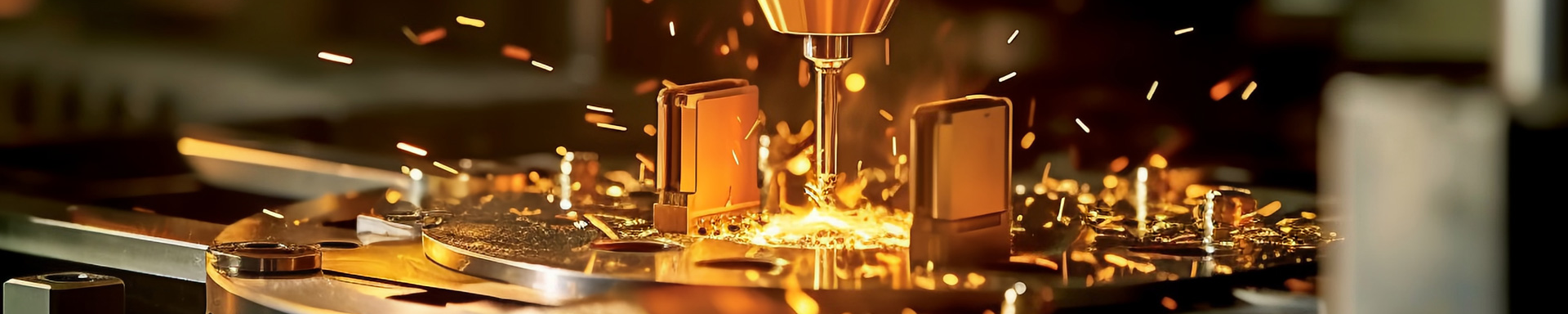
Understanding the Mechanics of Punching Stretching Mould Forming
2025-02-05 16:01The Punching Process: Initial Shape Definition
The process begins with punching, the initial step that defines the overall shape of the final product. This involves a precisely shaped punch that pierces the sheet metal, creating holes or cutouts. The punch's geometry, coupled with the sheet material's properties (thickness, tensile strength, yield strength, etc.), determines the accuracy and quality of the cut. Imperfect punching can lead to burrs, cracks, or dimensional inaccuracies, impacting the subsequent stretching and moulding stages. Factors influencing the punching operation include punch and die clearance, applied force, and lubrication. Insufficient clearance can result in excessive friction and tearing, while excessive clearance produces ragged edges. The material's ductility plays a crucial role; highly ductile materials are more prone to stretching during punching, whereas brittle materials are more likely to fracture.
Furthermore, the design of the punch itself is paramount. Sharp punches minimize the bending radius at the cut edge, reducing the risk of tearing, while punches with rounded edges provide smoother cuts but potentially at the expense of precision. The choice of punch geometry should carefully consider the desired edge quality and material properties. The force required for punching is also dependent on the shear strength of the material and the area being punched. Careful control of this force is critical to prevent damage to the punch or the sheet metal.
Stretching: Shaping the Metal
Following punching, the sheet metal undergoes stretching, a crucial phase that transforms the flat blank into a more complex three-dimensional shape. This process involves applying tensile forces to the sheet metal, causing plastic deformation beyond its yield point. The stretching is often guided by a die, which provides the desired contour. The amount and direction of the stretching are precisely controlled to avoid failure of the sheet. Factors influencing the stretching process include the material's strain hardening exponent (n-value), which determines its resistance to further deformation, and its r-value (anisotropy), which describes the directionality of the material's strength.
Uniform stretching is key to preventing localized thinning or necking, which can lead to defects and failure. Therefore, the design of the stretching die, including its radius and geometry, plays a significant role in achieving uniform deformation. The force required for stretching increases as the deformation progresses due to strain hardening. Precise control of the stretching force is crucial to prevent excessive thinning or rupturing. Finite element analysis (FEA) is often used to simulate the stretching process and optimize the die design for improved efficiency and product quality.
Mould Forming: Final Shape Refinement
The final stage, mould forming, refines the shape further, often incorporating intricate details and precise dimensions. This involves pressing the stretched sheet metal into a precisely machined mould, which imparts the final shape. The pressure and temperature applied during this phase are carefully controlled to prevent springback (elastic recovery) and ensure dimensional accuracy. This stage may also involve additional operations such as trimming or embossing to achieve the desired surface finish and features.
Mould forming relies heavily on the material's elastic and plastic properties, its ability to conform to the mould cavity under pressure, and the mould's own geometry. Insufficient pressure can lead to incomplete filling of the mould, resulting in inaccuracies. Excessive pressure may cause material thinning, tearing or even cracking. The design of the mould, including its geometry, surface finish, and material, directly influences the quality of the final product. Advanced simulation techniques like FEA are used to optimize the moulding process, predict potential issues, and minimize the need for costly trial-and-error experimentation.
Material Properties and Process Optimization
The success of punching, stretching, and mould forming hinges on a comprehensive understanding of the sheet metal's mechanical properties. Factors like yield strength, tensile strength, ductility, anisotropy, and strain hardening exponent significantly impact the formability of the material and the feasibility of the process. The chosen material needs to be sufficiently strong to withstand the forces involved but also ductile enough to undergo the necessary deformations without fracture. Improper selection of materials leads to defects, increased costs, and production inefficiencies.
Optimizing the process involves a careful consideration of all these factors, often leveraging advanced simulation techniques and experimental testing. Process parameters such as punch and die geometry, applied forces, temperature, and lubrication are meticulously adjusted to achieve the desired results. By integrating simulation with experimental validation, engineers can develop robust and efficient processes, producing high-quality products while minimizing waste and maximizing productivity.