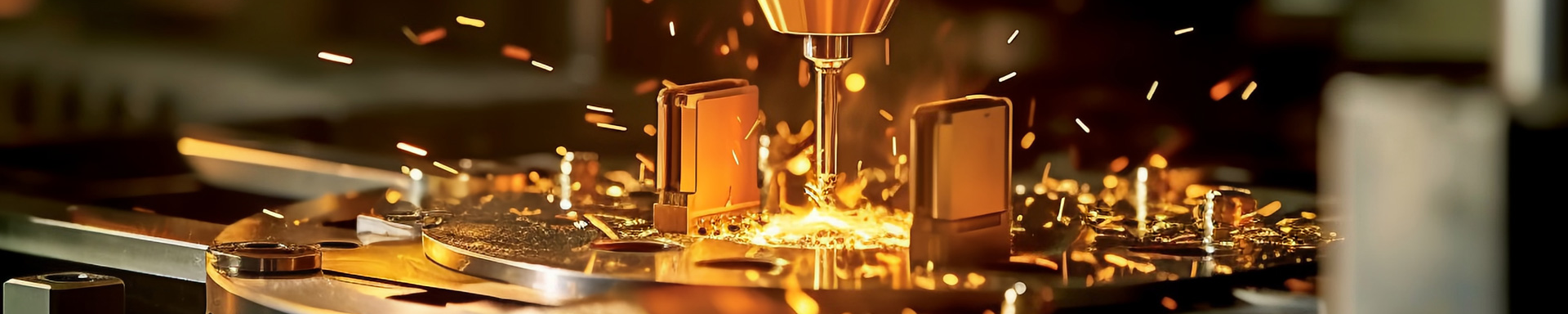
- Home
- >
News
Understanding the mechanics of punching stretching mould forming is crucial for anyone involved in sheet metal forming, a process vital in numerous industries, from automotive manufacturing to consumer electronics. This process, characterized by its ability to create complex three-dimensional shapes from flat sheet metal, relies on a sophisticated interplay of forces and material behavior. This article delves into the intricacies of this process, examining the underlying mechanics that govern its success and limitations. Understanding these mechanics allows for optimized process parameters, improved product quality, and reduced material waste.
The relentless pursuit of higher production rates, improved product quality, and reduced manufacturing costs drives continuous innovation in the metal forming industry. Punching and stretching, crucial processes in producing complex sheet metal parts for automotive, electronics, and appliance sectors, rely heavily on the performance and efficiency of their dedicated molds. Optimizing these molds is not just about increasing throughput; it's about achieving a delicate balance between speed, precision, and tool longevity, ultimately contributing to significant cost savings and enhanced competitiveness. This exploration delves into the multifaceted strategies for maximizing the performance and efficiency of punching and stretching molds.