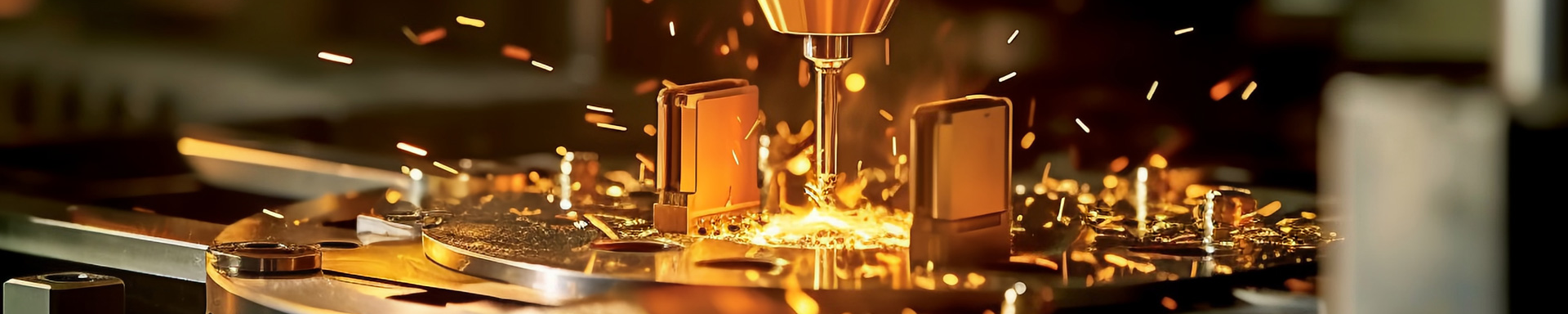
Discover Versatile Aluminum Extrusion Profiles Endless Options
2025-01-22 16:47Unparalleled Design Flexibility
The fundamental advantage of aluminum extrusion is its capacity to be molded into virtually any conceivable shape. This is achieved through a process where heated aluminum is forced through a precisely engineered die, resulting in a profile that mirrors the die's design. This allows for the creation of intricate geometries, including channels, slots, holes, and complex curves, all within a single extrusion. This level of design freedom is unparalleled by many other manufacturing processes, enabling engineers to optimize designs for specific functional and aesthetic requirements.
Furthermore, this flexibility extends beyond simple shapes. Aluminum extrusions can incorporate various features directly into the profile during the extrusion process. This includes integrated fasteners, ribs for structural reinforcement, and even complex internal passages for fluid or wiring routing. This integrated design approach minimizes the need for secondary machining and assembly, streamlining production and reducing costs.
Exceptional Strength and Durability
Aluminum's inherent properties contribute significantly to the exceptional strength and durability of extruded profiles. Its high strength-to-weight ratio makes it an ideal material for applications where weight reduction is critical, such as in aerospace and automotive industries. This lightweight yet robust nature allows for the creation of strong structural components without compromising on performance or efficiency.
Beyond strength, aluminum extrusions also exhibit excellent corrosion resistance, particularly when anodized or powder-coated. This protective layer significantly extends the lifespan of the profiles, making them suitable for both indoor and outdoor applications, even in harsh environments. This durability contributes to a lower overall lifecycle cost compared to many alternative materials.
Wide Range of Applications
The versatility of aluminum extrusion profiles translates into a staggering array of applications across diverse sectors. In the construction industry, they form the basis of window frames, curtain walls, and various structural components. Their lightweight yet sturdy nature makes them ideal for building facades and interior designs, offering both aesthetic appeal and structural integrity.
The automotive industry utilizes aluminum extrusions extensively for creating lightweight chassis components, body panels, and interior trim. This contributes to improved fuel efficiency and enhanced vehicle performance. Similarly, the aerospace industry leverages aluminum extrusions for lightweight yet strong structural parts in aircraft and spacecraft, where weight reduction is paramount.
Beyond these major sectors, aluminum extrusions find application in consumer electronics, industrial machinery, furniture manufacturing, and numerous other fields. Their ability to be easily customized, combined with their strength and durability, makes them a versatile solution for a wide spectrum of needs.
Customization and Finishing Options
The process of aluminum extrusion allows for a high degree of customization. Beyond the shape of the profile itself, various surface treatments and finishing options are available to enhance the aesthetic appeal and performance of the final product. Anodizing provides a durable, corrosion-resistant finish, while powder coating offers a wider range of colors and textures.
Furthermore, the ability to incorporate custom features during the extrusion process further enhances customization. This includes the addition of specific slots, holes, or other features designed to meet the unique requirements of a particular application. This level of customization allows for a truly bespoke solution, tailored to the precise needs of the customer.
Cost-Effectiveness and Sustainability
While the initial investment in custom tooling for aluminum extrusion might seem significant, the long-term cost-effectiveness is undeniable. The efficient manufacturing process, reduced need for secondary machining, and enhanced durability contribute to a lower overall lifecycle cost compared to other materials. Furthermore, aluminum is a highly recyclable material, promoting sustainability and minimizing environmental impact.
The combination of design flexibility, strength, durability, and cost-effectiveness makes aluminum extrusion profiles a compelling choice for a vast array of applications. The nearly endless options available ensure that there is an ideal solution for virtually any design challenge, contributing to its widespread adoption across diverse industries and applications.