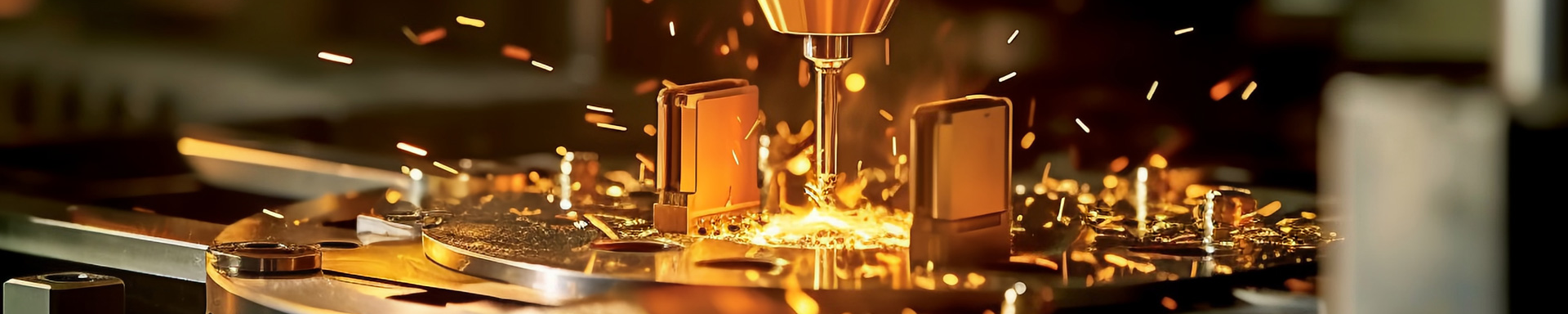
News
The skies above us are a testament to human ingenuity, a marvel of engineering pushing the boundaries of what's possible. But behind the gleaming metal and advanced technology of modern aircraft lies a network of crucial components, often overlooked, that ensure safety and operational efficiency. Among these unsung heroes are high-quality aircraft rubber parts. These seemingly simple components play a vital role, contributing significantly to the longevity and performance of aircraft. From sealing critical systems to absorbing vibrations and damping shocks, their importance is undeniable, and the demand for high quality in their manufacture is paramount. This exploration delves into the world of high-quality aircraft rubber parts, examining the critical factors that define their superior performance and the significant impact they have on the aviation industry.
The aviation industry demands unwavering reliability and precision, and this extends to even the smallest components. Hidden within the complex machinery of aircraft are countless rubber products, critical to performance, safety, and longevity. These specialized parts, far from being simple seals or gaskets, represent sophisticated engineering feats designed to withstand extreme temperatures, pressures, and demanding operational conditions. Understanding the intricacies of supplying these crucial components is key to grasping the importance of a reliable source like Top Aircraft Rubber Product Supply. For decades, companies like Top Aircraft Rubber Product Supply have been instrumental in ensuring the smooth and safe operation of aircraft worldwide, fulfilling the rigorous demands of a highly regulated industry. This exploration will delve into the key aspects that define a leading supplier in this critical sector.
Precision shape punch die inserts represent a crucial component in the world of metal stamping, a process vital to countless industries. From the intricate components of electronics to the robust parts of automobiles, metal stamping relies on precise and efficient tooling to achieve consistent, high-quality results. These inserts, small yet mighty, are the heart of that tooling, defining the shape and accuracy of the final product. Understanding their function and capabilities is crucial for anyone involved in manufacturing or design using metal stamping techniques.
Custom shape punch die inserts represent a significant advancement in the world of precision metal stamping. They offer manufacturers unparalleled flexibility and efficiency in producing parts with intricate and complex geometries, far exceeding the capabilities of standard punches. Imagine needing to create a component with a uniquely shaped hole, a specific curve, or a complex internal feature – a task that would be incredibly difficult, time-consuming, and expensive with traditional methods. Custom shape punch die inserts provide a streamlined and cost-effective solution, allowing for the precise creation of these otherwise challenging designs. This article delves into the various aspects of these inserts, exploring their benefits, applications, and considerations for their effective utilization.
The automotive industry is in a constant state of evolution, driven by the relentless pursuit of lighter, stronger, and more fuel-efficient vehicles.
High-pressure die casting (HPDC) remains a cornerstone of automotive component production, prized for its speed and ability to create intricate parts. However, traditional HPDC often struggles with achieving consistent dimensional accuracy and surface quality across large batches.
The relentless pursuit of efficiency and quality in manufacturing has propelled the need for comprehensive guides dedicated to optimizing complex processes. One such process, crucial to countless industries, is injection molding.
Explore the world of precision molding injection is a journey into the heart of manufacturing, where intricate designs meet high-tech machinery to create parts with unparalleled accuracy and complexity. From the minuscule components within a smartphone to the robust structural elements of a car, precision molding injection shapes our modern world.
High-quality molding injection is a cornerstone of modern manufacturing, enabling the mass production of intricate and precise parts across a vast range of industries. From the tiny components within your smartphone to the robust casings of automotive engines, injection molding's versatility and efficiency are unmatched.
Understanding the benefits of injection molding requires delving into a manufacturing process that has revolutionized countless industries. From the ubiquitous plastic bottle to intricate automotive components, injection molding's versatility and efficiency have made it a cornerstone of modern manufacturing. This exploration will unveil the key advantages this method offers, highlighting its impact on cost, quality, and overall production efficiency.