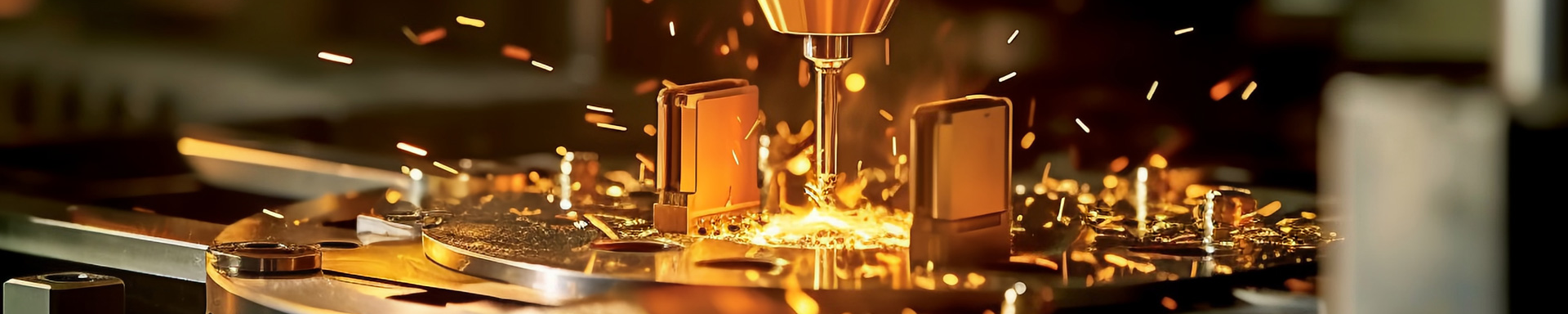
- Home
- >
News
Advanced punching and shearing die design is a critical aspect of modern manufacturing, impacting product quality, production efficiency, and overall profitability. This intricate process involves creating specialized tooling to precisely cut and form sheet metal components, ranging from simple shapes to highly complex geometries. Understanding advanced techniques in this field is crucial for engineers and designers seeking to optimize their manufacturing processes and achieve superior results. This article delves into several key aspects of advanced punching and shearing die design, highlighting innovative strategies and considerations for optimal performance.
The relentless pursuit of efficiency and precision in manufacturing has driven significant innovation in the field of punching and shearing dies. These fundamental tools, used to cut and shape sheet metal, are undergoing a transformation, moving beyond traditional designs to incorporate advanced materials, geometries, and manufacturing processes. This evolution is crucial for industries ranging from automotive and aerospace to electronics and construction, where the demand for higher production rates, improved part quality, and reduced costs is constantly increasing. This exploration delves into innovative solutions reshaping the landscape of punching and shearing die technology, examining advancements that are not only enhancing performance but also promoting sustainability and flexibility.
High-precision punching and shearing die manufacturing is a critical process in numerous industries, ranging from automotive and aerospace to electronics and medical devices. These dies, sophisticated tools used in stamping processes, are responsible for creating intricate shapes and precise cuts in sheet metal with exceptional accuracy. The demand for smaller, lighter, and more complex components has driven a relentless pursuit of higher precision in die manufacturing, pushing the boundaries of engineering and manufacturing technology. The intricate nature of these dies, demanding tolerances measured in microns, highlights the specialized expertise and advanced machinery required for their creation. This exploration delves into the intricacies of high-precision punching and shearing die manufacturing, shedding light on the key aspects that contribute to its precision and efficiency.
Punching and shearing dies are fundamental tools in sheet metal fabrication, used to create precise holes and cut shapes from metal sheets. Their efficiency and longevity directly impact production costs and overall manufacturing success. Optimizing their performance, therefore, is crucial for any manufacturer striving for competitiveness. This involves a multifaceted approach encompassing material selection, die design, and operational practices. Understanding these elements allows for the creation of robust, productive, and cost-effective punching and shearing processes. This exploration will delve into the key strategies for optimizing the performance of these vital tools.
The world of manufacturing is constantly evolving, driven by the relentless pursuit of efficiency, precision, and cost-effectiveness. At the heart of many manufacturing processes lies the humble, yet crucial, punching and shearing die. These seemingly simple tools are responsible for shaping countless products we use daily, from automotive parts and electronic components to intricate medical devices. Recent advancements in die technology have significantly impacted the industry, unlocking new levels of performance and capability. This exploration dives into the latest innovations shaping the future of punching and shearing die technology.
Understanding Punching and Shearing Die Processes is crucial for anyone involved in sheet metal fabrication. These processes, fundamental to manufacturing a vast array of products from automotive parts to electronics components, involve the precise application of force to cut and shape metal sheets. This understanding extends beyond simply knowing *what* happens; it delves into the intricacies of tool design, material selection, and process optimization for achieving high-quality, consistent results. A thorough grasp of these processes is vital for ensuring product quality, maximizing production efficiency, and minimizing waste. This exploration will delve into the mechanics, applications, and considerations involved in both punching and shearing.
Cost-effective manufacturing is paramount in today's competitive industrial landscape. For businesses relying on sheet metal fabrication, the design and implementation of punching and shearing dies play a crucial role in determining overall production efficiency and profitability. High-quality, yet affordable, punching and shearing die solutions are no longer a luxury; they're a necessity for maintaining a competitive edge. This exploration delves into various strategies and considerations for achieving cost-effective punching and shearing die solutions, highlighting the balance between initial investment, long-term performance, and overall return on investment (ROI).
Punching and shearing dies are crucial components in numerous manufacturing processes, playing a vital role in shaping sheet metal into a vast array of products. From automotive parts and electronics to appliances and construction materials, these dies are essential for creating precise cuts and shapes with high speed and accuracy. However, the effectiveness of any manufacturing process hinges significantly on the durability and efficiency of its tooling. This article delves into the critical factors influencing the lifespan and productivity of punching and shearing dies, examining the materials, design considerations, and operational practices that contribute to optimal performance. Understanding these aspects is key to minimizing downtime, reducing costs, and maintaining consistent product quality.